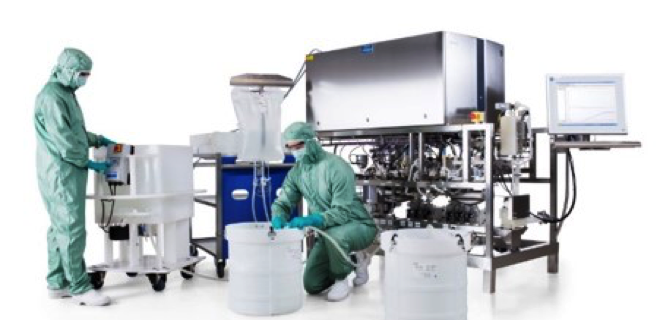
Addressing Buffer Bottlenecks using automated In-line conditioning and ready-made stock solutions for mAb processes
Multiple buffers in a wide range of formulations are required to produce a single biopharmaceutical. Because of the large volumes required, buffer preparation can easily become a bottleneck in production. Traditionally, buffers are prepared manually in the volume needed according to specific recipes. Due to the large quantities used, buffer management requires careful planning and considerable floor space is required for the preparation and storage of such large buffer quantities. In addition to high labor and facility space cost, there is a risk of human error and variability associated with such a time-intensive manual activity. Buffer variability can affect both quantity and quality of the final product.
At the recent American Chemical Society (ACS) national meeting in San Francisco, California, a poster titled, “In-line conditioning using ready-made stock solutions in a mAb process step,” presented a solution that automates the buffer preparation using pre-made stock concentrates connected to an Inline Conditioning system, thus reducing the opportunity for a bottleneck to occur.
In this set up, ready-made stock solutions delivered in disposable bags, were used to prepare typical Protein A chromatography buffers for purification of monoclonal antibodies (mAb). The stock solutions were connected directly to the Inline Conditioning system and both phosphate and acetate buffers, as well as solutions for acid strip and alkaline cleaning in place (CIP), were produced according to a predefined protocol in the control software. The Inline Conditioning system’s ability to produce correct buffers and handle the buffer switch transition was tested by having the system prepare the buffers/solutions sequentially by changing the pump inlets to simulate a Protein A chromatography run with continuous buffer preparation.
Dynamic control to ensure correct buffer formulations
The Inline Conditioning system features built-in dynamic control functionality to adapt to incoming variability and to produce consistent results. Dynamic control carefully monitors the effects of ion activity as well as concentrations in stock solutions and final buffer. This system ensures quality control of the final buffer formulation by compensating for any buffer variability using in-line adjustment of relative volumes. The dynamic control functionality of the Inline conditioning system uses feedback loops for pH and conductivity to ensure production of the final buffer at the required strength and pH.
In-line conditioning vs in-line dilution
In-line dilution means diluting concentrated buffers with water. The subsequent dilution will cause pH and conductivity shifts that need to be taken into consideration in the final buffer formulation. In-line conditioning means buffers are formulated using concentrated stock solutions of the required acid, base, WFI, and salt. A wide range of buffer concentration and pH solutions can be created. Conductivity and pH adjustments are automatically done throughout the process.
With in-line dilution, one buffer concentrate is required to produce one final buffer. As buffers are multi-component formulations, the common ion effect will limit concentration grade when preparing stock solutions. The least soluble ion will determine the maximum concentration of the stock solution. This limitation is avoided with in-line conditioning as single-component stock solutions are used. Compared to in-line dilution solutions, the stock solutions have higher concentrations and smaller volumes.
Summary
At the ACS meeting in San Francisco, a solution which automates buffer preparation was presented. In this setup, an Inline Conditioning system was used to automatically prepare typical Protein A chromatography buffers for purification of monoclonal antibodies (mAb), in a sequential manner. Automation both saves time and minimizes the error risk with manual buffer preparation, ensuring consistency between batches. The built-in dynamic control functionality assures the accuracy of the buffers produced. In addition, using ready-made, highly concentrated, low-volume stock solutions, further increases efficiency by saving time and space in buffer preparation and minimizing the need for raw material qualification.
To see the full data, please click on the poster below:
Interested to learn more? Read this application note, “Overcoming buffer challenges with in-line conditioning”
For more on Downstream Bioprocess Efficiency, please see:
https://downstreamcolumn.com/increasing-downstream-bioprocess-efficiency-overcoming-bottlenecks/