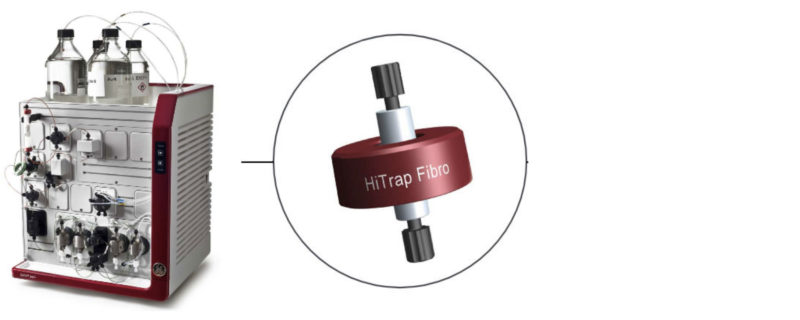
Addressing Downstream Throughput Bottlenecks with Rapid Cycling Protein A Based Fiber Chromatography
Faster process times and increased flexibility in manufacturing continue to be key drivers in both upstream and downstream processing. New technologies are needed to address bottlenecks and to infuse more flexibility in process development and manufacturing. For downstream, chromatography purification can be a resource intensive step and a source of bottlenecks due to decreased throughput.
While improvements in Protein A chromatography resins, such as high capacity resins, provide much better capacity, low flow rates are still a potential source of slow downs. One alternative solution for addressing areas where increased throughput and flexibility is required is the use of Fiber based chromatography.
Fibro PrismA is a protein A fiber chromatography format developed to complement traditional resin-based chromatography. The protein A fiber matrix has an open pore structure where mass transfer is governed by convective flow. This structure allows high mAb binding capacities at very short residence times, which reduces cycle times to minutes instead of the hours needed for resin-based chromatography.
These short cycle times enable high-throughput purification of mAbs and opportunities for significant time savings in process development. At a larger scale, the protein A fiber in rapid cycling operation allows full utilization of the protein A lifetime during one batch as well as cost-effective single-use chromatography.
A recent webinar, “Rapid cycling protein A based fiber chromatography to address emerging downstream bottlenecks,” presented by Oliver Hardick, Business Leader, Cytiva, provides examples of how Fibro PrismA technology can help to optimize wash and elution buffers in downstream process development and reduce development times. They also discuss how this scalable technology enhances productivity at process scale. Highlights of the webinar are provided below.
Biomanufacturing Landscape
Dr. Hardick began the webinar by discussing the global trend in biomanufacturing to focus on smaller, more targeted patient populations. This move has resulted in the use of smaller batch sizes with the estimated annual production of the majority of commercial mAbs to be under 100 kg/yr. Manufacturing smaller batch sizes increases the need for multiproduct facilities and flexible manufacturing solutions like single use technologies.
He went on to talk about how this relates to chromatography and discussed how chromatography beads have met industry needs for the past six decades (Figure 1). However, a new chromatography paradigm is needed to meet new demands for increased flexibility and multiproduct facilities. This includes incorporating single-use technologies for chromatography. He stated that resins and Fibro chromatography compliment each other and can be used in tandem based on process needs.
Fibro Unit Options
Oliver explained that Fibro units are available in the HiTrap™ Fibro PrismA and HiScreen™ Fibro PrismA for research and process development purposes. HiScreen units can typically complete a full cycle with CIP in less than 5 minutes, with HiTrap it can be reduced to as low as 2-3 minutes. This is a big difference compared to resin that takes several hours. With these cycle times, experimental throughput can be increased 20 fold, thereby cutting lead times and increasing process robustness. For example a full life time study can be completed in a single day and early in process development.
He shared that clinical and commercial manufacturing Fibro options are planned for launch in the first half of 2021 with capacity for up to 2,000 liter bioreactors. In clinical manufacturing, they have found that Protein A consumable costs can be reduced by up to 85%. These fast cycle times enable full unit utilization in a single batch increasing productivity up to 400 g/L/h. This eliminates lengthy changeovers with true cost-efficient single-use chromatography.
Fibro PrismA Technology Highlights
Oliver explained that with Protein A resins, mass transfer of target proteins is restricted by diffusion, The diffusion into the porous structure results in a flow-rate-limited operation, which presents a fundamental barrier to improving purification productivity. Instead, the structure of the fibers in the Fibro technology is highly open to facilitate mass transfer without diffusion, like membrane and monolith technologies, but it also yields a high surface area (Figure 2). This enables purification cycles of around 5 minutes, as opposed to the traditional hours.
Flexibility – Decreased Process Times or Reduction in Absorbent Volume
The high flow rates and high binding capacities enable either decreased process times or the use of rapid cycling to decrease fiber adsorbent volume required. This enables substantial process time reductions or consumable cost savings.
High Performance Across Antibody Variants
Oliver presented data demonstrating Fibro’s high binding capacity for multiple antibody variants with greater than 30 g/L for the majority of 27 evaluated mAbs and antibody variants (Figure 3).
Comparison with Resin
Fibro units use the high alkaline stable PrismA ligand that has been genetically engineered and optimized for high capacity and to tolerate high CIP sodium hydroxide concentrations. Since the ligand is doing the work, similar performance is seen between MabSelect and resin and Fibro PrismA. However, operationally, the two types of chromatography are quite different with key features compared in Figure 4.
Case Study – High-throughput Purification using Fibro PrismA Units for Early Upstream Process Development
Next, Oliver presented a case study that was done in collaboration with a company that needed purification of many samples in high-throughput. They needed to create a quick, automated mAb purification step for purification of multiple mAb samples produced in ambr™ 15 and ambr 250.
Study authors found that they could achieve substantial time savings with Fibro chromatography compared to resin-based chromatography. He shared that with Fibro, they could conduct 48 runs with 10 mL ambr samples in 3.6 hours vs. 44.8 hours with a resin column. With 250 mL ambr samples, 21 runs took 3.5 hours using the Fibro unit and 43.8 hours with the resin column (Figure 5).
Next they compared time savings with Fibro chromatography to a Tecan RoboColumn operation. They found that using the Fibro units plus an autosampler took 80 minutes to process 8 runs and with the Tecan RoboColum and a MabSelect SuRe RoboColumn resin it took 120 minutes to complete 8 runs (Figure 6).
Oliver explained that with the Fibro technology enables flexible chromatography options for multiproduct facilities and allows a company to choose between single-use operation and faster process times. In one study, Fibro chromatography was used to purify 7 kg of mAb from a 2,000 liter bioreactor run with either a single-use approach or a faster process time approach. When the Fibro Unit was operated as a single-use batch operation, 194 cycles per batch were purified and the process took 19 hours. When the operation was switched to short process time, a larger Fibro unit was used and 97 cycles per batch were purified with 9.5 hours of processing time. This demonstrates how companies can choose the processing mode that best fits their product and facility needs (Figure 7).
Scalability
Oliver presented data conducted by a third party demonstrating the ease of scalability for Fibro units. There are scale-up options for Fibro and AKTA systems for every stage from research to process (Figure 8).
Summary
In closing, the Fibro units offer new flexibility and cost efficiency throughout multiple stages of product development. They compliment resin-based chromatography by providing benefits that resin-based chromatography doesn’t offer. In research and process development, Fibro’s faster purification can reduce development timelines. In clinical development, cost can be reduced by utilizing Fibro’s full Protein A lifetime in one batch. In manufacturing, Fibro’s cost-efficient single-use chromatography delivers more batches per year and allows large capital chromatography investments to be delayed until financial risks are reduced.
To learn more on Fibro technology and evaluate the technology visit the new Fibro chromatography landing page