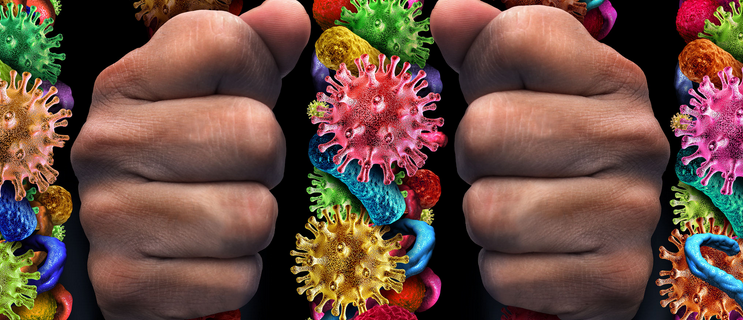
Cost and impact of a bioburden incident
Manufacturing biologicals is tricky. A major concern is the risk of microbial contamination, jeopardizing product safety and causing high costs. But there are solutions for decreasing the risks.
Making monoclonal antibody (mAb) drugs? Safety first
In releasing a biomedicine, the last thing a biopharma company wants is for people to be harmed. This makes the risk of bioburden, and how it can be prevented, a major issue for drug safety.
Thankfully, businesses and regulatory agencies share the same goal—to make every product safe and effective. Manufacturers and suppliers might have concerns with production economy, security of supply, and other operational issues, but their number one priority is always the health of the patient.
Bioburden management is key
A major area for safety improvement is bioburden management. High up on any list of critical quality attributes (CQAs) for mAbs, you will likely find a requirement for the absence of microbial contamination. Apart from the potentially tragic impact on patients, the economic consequences of a batch failure are enormous. For the mAb blockbusters, a month production stop can result in lost revenues of up to USD 1 billion. A typical QA investigation could cost USD 20 000. These are big and scary numbers (Table 1).
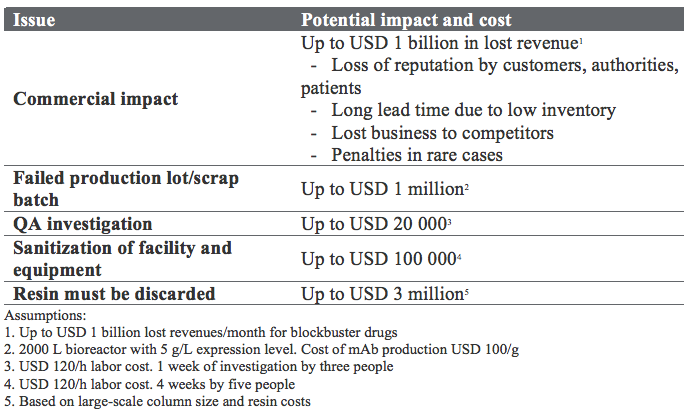
Because mAbs are always produced from living cells in complex processes, managing bioburden is a sizeable challenge. Filtration can make sure microbes are absent in the final product and using low pH elution during protein A capture chromatography can safeguard against some viruses. However, there are still many bioburden risks in both upstream and downstream bioprocessing (1). Recently, there have been some welcome developments. For example, single-use products have been introduced as a viable alternative to stainless steel equipment. This has resulted in greater simplicity and better control over routes for microbial contamination.
Whenever new approaches are introduced, there is an initial period where suppliers and users justify switching, based on experience and good science. Next comes a period where the new technologies are accepted, based on the pros and cons compared to previous options. In the case of single-use technology, choice is mainly influenced by the scale of operation and need for production flexibility.
Other factors to bear in mind include preferences regarding bioburden control, staff experience, and facility constraints. And, of course, there are costs to be accounted for. Where previously there would be concerns over disposal of cleaning agents, these are replaced by how to dispose of the single-use items. Costs for building and operating a traditional steel-piped plant are replaced by costs for raw materials such as larger warehouses and increased levels of inventory.
For more information about de-risking the production environment, please Click here to be directed to GE Healthcare Lifesciences BioMatters Blog