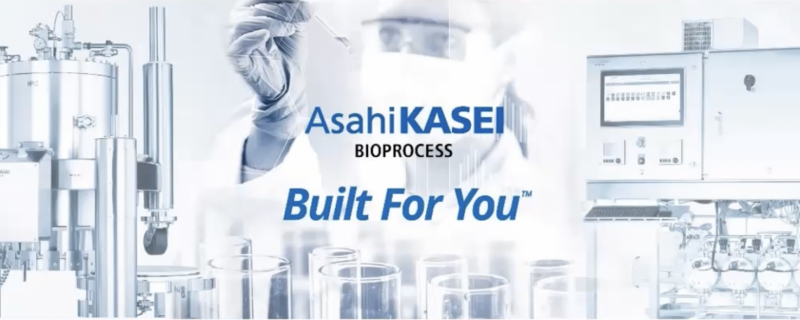
Getting the Most From Inline Buffer Formulation: MOTIV® Performance Data Review
Contributor:
In this mini-webinar Nainesh Shah, Sr. Application Engineer with Asahi Kasei discusses the benefits of inline buffer formulation and presents performance data on the MOTIV® inline buffer formulation system with case studies demonstrating the flexibility of MOTIV to create a wide variety of complex buffers.
The MOTIV System
The MOTIV system was originally launched in 2007 as IBD (Inline Buffer Dilution) and has since undergone several modifications and enhancements. In 2013, it evolved into a standard 3 pump system, with further improvements in 2015, including the addition of a reagent tracker for better chemical tracking. Subsequent upgrades in 2016 introduced a five pump system, and in 2018, larger custom units with six and seven pumps were developed. In 2020, IBD was officially renamed MOTIV, and in 2023, a single-use version of the system was launched to eliminate the need for SIP/CIP procedures.
MOTIV 3 is the 3-pump IBF system designed to produce dilute and conditioned buffers. The system operates by utilizing three streams, with one larger pump delivering the diluent (such as WFI or purified water) and two smaller pumps for buffer concentrate and acid/base modifiers.
MOTIV 5 is suitable to produce more complex buffers constructed from up to five streams. The system offers maximum flexibility for multi-component buffers using a combination of conductivity, pH, and mass flow control. It can achieve flow rates of up to 5,000 L/h encompassing a broad capacity range for process development to production scale batches.
MOTIV plus is the ideal system for non-standard situations. From custom flow rate ranges, specific materials of construction for corrosion resistance (e.g., AL6XN), additional pumps (>5 pump systems) and inline monitors, our AKBA experts can build you a system that will do exactly what you need.
MOTIV SU is a single use inline buffer formulation system, built to produce complex buffers on-demand effectively and efficiently, all from one pump head, and without the need for CIP/SIP procedures between batches.
As of last year, there were approximately 59 installations of the MOTIV system worldwide, with a majority in the USA and others evenly distributed across Europe, Asia, and China. The system is primarily used for preparing chromatography buffers for purification, dilution of cleaning-in-place (CIP) solutions, and various other applications such as molecular biology buffers.
Testing and data generation have been conducted to ensure the consistency and performance of the system, including dilutions of up to 20 times and monitoring of ramp-up times, process interruptions, pH, and conductivity control. Batch reports generated by the MOTIV system provide detailed insights into the production process, including waste versus product ratios and concentrate usage. Standard buffers that have been created in MOTIV and tested for performance are shown below.
How MOTIV Works
The MOTIV system operates on a base configuration of either a three-pump system MOTIV 3 or a five-pump system MOTIV 5. In MOTIV 3, one pump is dedicated to water dilution (P1), while the other two pumps (P2 and P3) control the addition of buffer concentrates. These components are mixed in a shear blender, with conductivity, pH, and flow monitored and controlled via a feedback loop to the pumps. The MOTIV 5 system follows a similar setup but with additional pumps (P4 and P5) for more complex buffer formulations.
The system is highly customizable, with options for varying flow rates and concentrations to meet specific requirements. It can handle a wide range of buffer formulations and operates within specified limits for pressure, temperature, and flow rate. The system is designed for flexibility in chemical selection, allowing users to adapt based on availability and supply chain considerations.
MOTIV Case Studies
Mr. Shah presents several case studies during the presentation that illustrate how the MOTIV system can be used to create various buffer solutions with different concentrations, pH levels, and conductivities. Testing and data analysis demonstrate the system’s consistency and reliability in producing accurate and stable buffer solutions over time.
Performance examples include consistent buffer production, process interruption recovery, pH and conductivity control, and scalability for both low and high flow rates. The system’s flexibility allows for customization based on chemical availability and user requirements, with comprehensive data logging and analysis capabilities.
Overall, MOTIV offers a user-friendly interface for method development and control, with options for batch reporting and data export for further analysis. It is designed to optimize productivity and efficiency in downstream processing for pharmaceutical and biotech applications.
About Asahi Kasei Bioprocess
Asahi Kasei’s Bioprocess division is committed to delivering advanced pharmaceutical manufacturing platforms, staying ahead of industry trends, and fostering long-term relationships with customers and vendors. The division encompasses purification, fluid management, safety testing services, and manufacturing, with a global presence spanning the USA, Europe, India, China, Brazil, and Korea. While virus filtration components are produced in Japan, the division’s main manufacturing facility in Glenview, IL, handles engineering, design, assembly, testing, and customer support. Quality and customer satisfaction are paramount, with ISO certifications and a focus on continuous improvement. The MOTIV inline formulation system, supported by the Ocelot operational software, is a key product offering in the fluid management category.