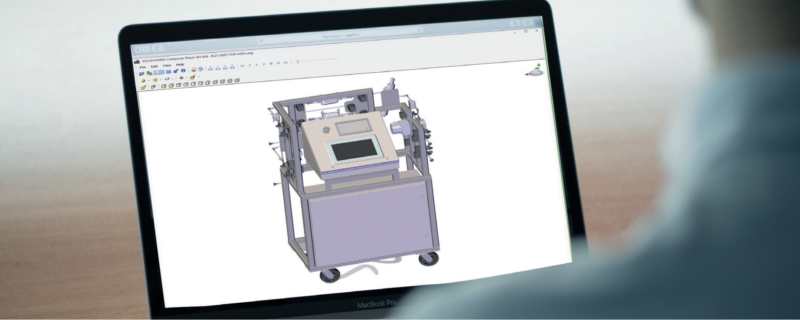
Agilitech Single-Use Tangential Flow Filtration (TFF) System for Biologics Manufacturing – A Case Study
Manufacturers in the biopharmaceutical industry are facing ever-expanding pipelines and the pressures to increase productivity and long-term sustainability while also rising to meet the challenges of new products with specialized processing requirements. This has led to increasing adoption of single use equipment into manufacturing workflows over traditional stainless-steel systems. While single use technology (SUT) designs have advanced for processes in both upstream and downstream unit operations, there are limitations to how tailored these units can be to fit the needs of a specific production process. Manufacturers are often required to adapt their process to what is commercially available resulting in technology solutions that may be suboptimal or unsustainable to meet future product demand. Those seeking more customization to a find ‘better fit’ are faced with piecemealing different components from different vendors into a contiguous system to achieve their production goals. Better engineering solutions are needed to create fit-for-purpose systems from the beginning that are cost-effective and scalable rather than the industry practice of reconfiguring standard systems. Addressing these gaps in process design requires thorough understanding of bioprocess requirements and equipment capabilities to build efficient processes to meet current production needs and ensure readiness to support future product growth.
Agilitech, a provider of SUT bioprocess equipment and engineering design and implementation services, recently published a case study describing its partnership with a biologics manufacturing company seeking an engineering solution to their existing tangential flow filtration system.
New Tangential Flow Filtration System Needed
THE PROBLEM: A leading manufacturer of enzymes for molecular biology applications required a new tangential flow filtration (TFF) system to support the commercial production of a cell-based product. Their existing system, which included a single-use bioreactor and TFF system, was suitable to meet production requirements initially, but demand for the product has grown significantly, which doubled the number of production runs needed to meet production targets. This not only increased their operating costs as more runs required more disposables, but also impeded the production of the company’s >400 other products. The company approached Agilitech to find an engineering solution to their TFF system that could maximize throughput in a cost-effective and timely manner while easing the stress on their workflow that could also be scalable to meet future production demands.
Custom Designed Fit-for-Purpose System
THE SOLUTION: Agilitech began by reviewing the company’s existing manufacturing process to identify the core challenge prior to designing a customized solution. The investigation revealed that the company was using a TFF system designed for flat sheet cassettes with hollow fiber cartridges that caused underlying problems in the existing process, where high pressure along the filter required operating at a reduced flow rate, which extended processing times. To solve the filtration problem and enable the company to reduce processing time, Agilitech’s bioprocessing and equipment experts collaborated with the company’s current filter supplier to identify a more suitable option that could accommodate higher pressures and flow rates to achieve better filtration volume throughput in a shorter processing time. Moreover, knowing the importance of designing a future-proof system, Agilitech experts recommended a more robust pump system that could handle flow-rate requirements for multiple size filters, building in the ability to upsize TFF capabilities to meet projected future capacity needs.
In the end, the Agilitech adapted its standard TFF system design to meet the customer’s specific needs for faster concentration and diafiltration of the cell-based product through changes that allow for higher flow rates, at higher pressures that maximize throughput and minimize processing time.
Agilitech addressed the process challenges and holistically to design a system with strategic forward-planning that not only served the needs of the company now but could easily adapt to meet future production requirements. The comprehensive design services leverage the deep technical expertise of their team to create customized, fit-for-purpose engineering solutions with the flexibility to accommodate changes as that process evolves. Understanding the supply chain challenges faced by the industry, Agilitech’s suite of single-use systems, are also designed to be brand agnostic with cross-functionality across source components from different vendors. This offers the customer more options, particularly when faced with supply chain issues of single-use components. Agilitech’s approach to product design offers a revolutionary new way for biomanufacturers to build better production systems right from the onset.
To download a copy of the case study, please visit: Case Study – Agilitech TFF System for Biologics Manufacturing