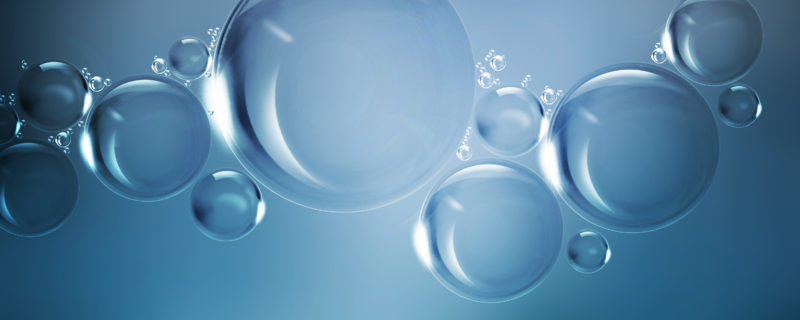
VEGA VEGAPOINT 21®– a non-contact probe for point level control in hygienic bubble traps
Gas bubbles in process fluids and buffer solutions are a common yet significant problem in bioprocessing because they can alter the microfluidic environment and negatively impact downstream chromatography steps. They can impede the flow through the resin column and limit contact with the resin in the resin bed, which can decrease separation efficiency and resolution. A hygienic bubble trap is a device that effectively separates gas bubbles from process fluids by allowing the bubbles to rise to the top of the fluid (Figure 1). Effective separation of gas bubbles relies on accurate monitoring and control of the fluid level in the bubble trap—this is where level sensors come in. The working volume of a bubble trap is typically 60-80% of its total volume, and the fluid should have a residence time of approximately 15 seconds. If the level is too low, the gas bubbles don’t have sufficient residence time to be effectively removed from the process fluid and the bubbles may pass with the process fluid through the bubble trap outlet. Conversely, if the level of the fluid is too high, fluid and bubbles can be drawn into the gas vent line and cause problems with contamination.
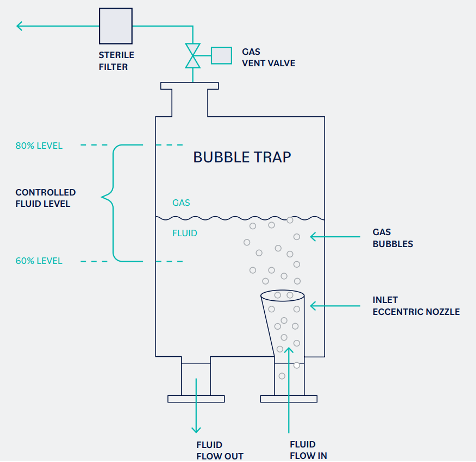
Point level sensor technologies are utilized to open and close the bubble trap gas vent valve to maintain fluid levels within the optimum volume range. When fluid levels drop below a low-level probe, the gas vent valve opens to allow gas to exit and the fluid level to increase. Once the fluid level reaches the high-level probe, the gas vent valve can be closed. A variety of sensors are used in the industry, and they can be broadly divided into two categories: direct process contact, and non-process contact technologies. While each sensor technology has its own merits and shortcomings, all non-process contact technologies have the advantage over direct contact technologies because they don’t make physical contact with the process fluid. This means they are not subject to the same regulatory requirements and risk assessments as contact technologies (i.e., cleanability, sterilizability, sensor extractables and leachables). A recently released application note from Agilitech evaluates the efficacy of a non-process contact sensor—the VEGA VEGAPOINT 21® capacitance point level probe—on an LJ Star® Hygienic Bubble Trap for point level control.
Testing the Efficacy and Reliability of the VEGAPOINT21® Capacitance Sensor
To evaluate the performance of the VEGAPOINT 21® capacitance sensors for fluid level control, two were mounted to the exterior of an LJ Star® Hygienic Bubble Trap as low- and high-level probes (Figure 2). The proximity to the process fluid of the capacitance sensor through the borosilicate glass wall can detect differences in dielectric field between the glass/air and that of the glass/process fluid. This capacitance change can activate the switch output and signifies the fluid level at that sensor point. In typical purification processes, the dielectric constant of water and buffer solutions is significantly higher than that of air and glass:
- Dielectric constant of Water for Injection (WFI) is approximately 15
- Dielectric constant of buffer solutions is typically > 50
- Distilled water has a dielectric constant of approximately 80
The dielectric constants of borosilicate glass and air is 5 and 1, respectively. In this evaluation, distilled water was used.
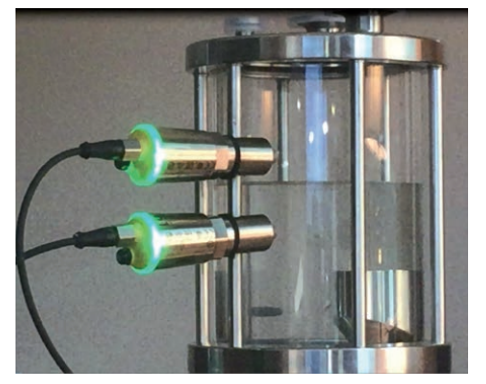
The units for the VEGAPOINT 21® capacitance point level switch are “% Resonant Frequency”. Based on differences between the process fluid in the bubble trap (distilled water), the optimal settings for the Switching Point (SP) and Reset Point (RP) were determined to be 83.0% and 84.0% Resonant Frequency (RF), respectively. This difference between the SP and RP is the hysteresis value. The details of how the VEGAPOINT 21® capacitance point level switch was configured using PACTware® are outlined in the application note.
In the actual test, the % RF of distilled water in the bubble trap detected by the probe is 83%. When the fluid level is below the point level probe, where the probe is detecting air, the % RF is 87%. This indicates that the % RF increases when the probe tip detects a low dielectric fluid (air) and decreases in the presence of a high dielectric fluid, such as distilled water. Therefore, any % RF below 83% is a result of the probe sensing a fluid and if the % RF is above 84%, the point level probe is sensing air. The 1% hysteresis value corresponds to about 1/8” (3mm) level difference based on the physical mounting position of the probes on the exterior of the bubble trap. The mounting of the probe was found to be an important factor in the repeatability of the sensed probe level and configuration parameters must be precisely tuned.
The results of the study demonstrate that the VEGAPOINT 21® probe is an effective and reliable approach for controlling point level. Because the probe can be mounted to a bubble trap of any size, and be easily integrated with existing equipment, it is an efficient and scalable method for controlling and optimizing the operation of the hygienic bubble trap as a vital element in the purification process suitable for a wide range of bioprocess applications.
To download a copy of the Agilitech white paper, please visit: Evaluation of Non-Process Contact Capacitance Point Level Measurements on the Outside of Hygienic Bubble Traps