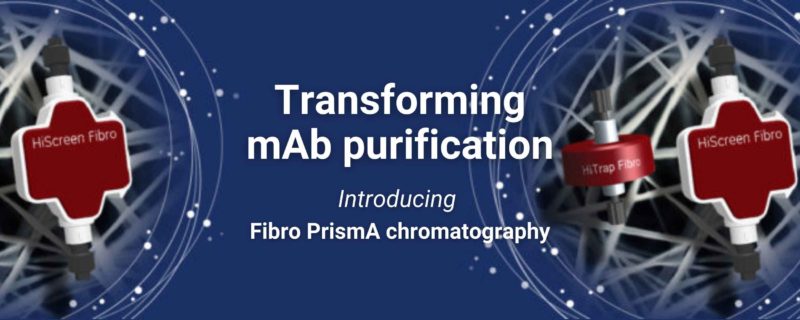
Cellulose Fiber-based Chromatography Increases Flexibility and Throughput in Antibody Purification
Recent industry initiatives have put increased emphasis on improving the flexibility and throughput of biomanufacturing processes. To achieve this, new technologies are required that permit faster process times and increased flexibility for a variety of manufacturing scenarios including smaller batch sizes and multi-product facilities. One critical aspect of the biomanufacturing process is downstream chromatography purification and this can often be a time and resource intensive step.
Protein A chromatography resins have been an important part of monoclonal antibody purification for decades. While recent high capacity Protein A resins offer significant improvements, there is still a need for alternative solutions to address areas where increased throughput and flexibility is required. One alternative is Fibro technology, which utilizes the high flow rates and high capacities of cellulose fiber to improve productivity, throughput and flexibility, while maintaining quality. HiTrapTM Fibro PrismA and HiScreenTM Fibro PrismA have recently been launched by Cytiva for applications in research and process development. Scale-up versions for pilot and process applications are expected first half of 2021.
How Fibro Technology Works
With Protein A resins mass transfer of target proteins is restricted by diffusion, The diffusion into the porous structure results in a flow-rate-limited operation, which presents a fundamental barrier to improving purification productivity. Instead, the structure of the fibers in the Fibro technology is highly open to facilitate mass transfer without diffusion, like membrane and monolith technologies, but it also yields a high surface area (Fig 1). This is a result of its manufacturing method, an additive process known as electrospinning (Fig 1,2). These unique features of Fibro allow it to obtain binding capacities of more than 30 mg/mL (Fig 3) in seconds of residence time rather than minutes as with conventional resin-based chromatography. This enables purification cycles of around 5 minutes, as opposed to the traditional hours.
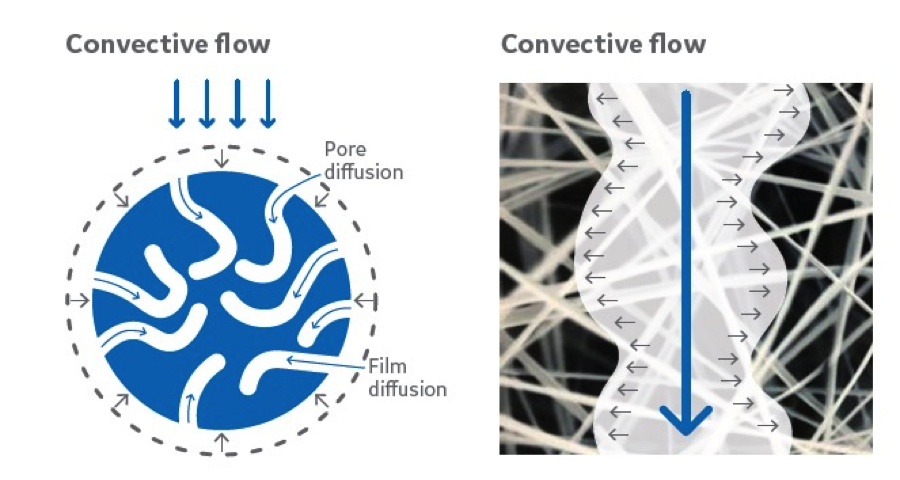
The open structure in Fibro fibers (right) allows convective flow and direct mass
transfer of the target protein to the ligand immobilized on the fiber surface
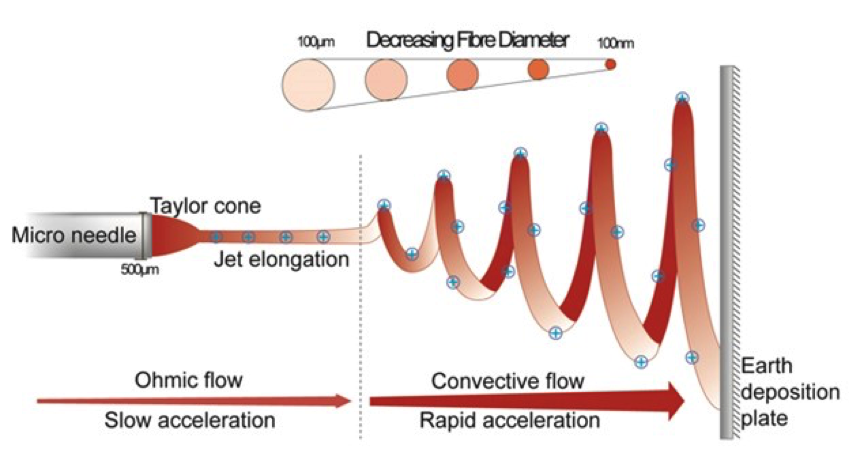
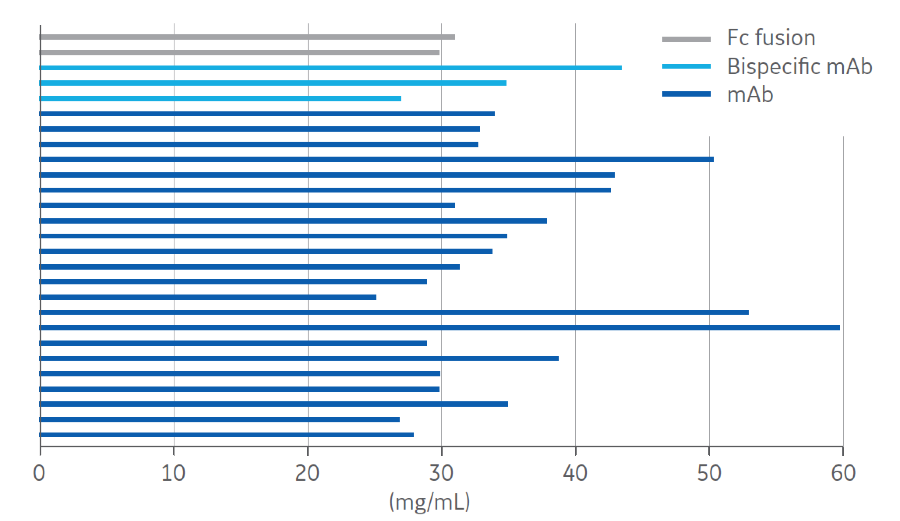
matrix for a variety of mAbs and antibody variants.
Key Advantages of Fibro Technology
Faster Cycle Times
Fibro has the ability to operate at shorter residence times, which significantly reduces cycle times. For example, a Fibro cycle can be completed in 5 minutes compared to 1 to 5 hours to perform a cycle on a resin-based chromatography column (Fig 4).
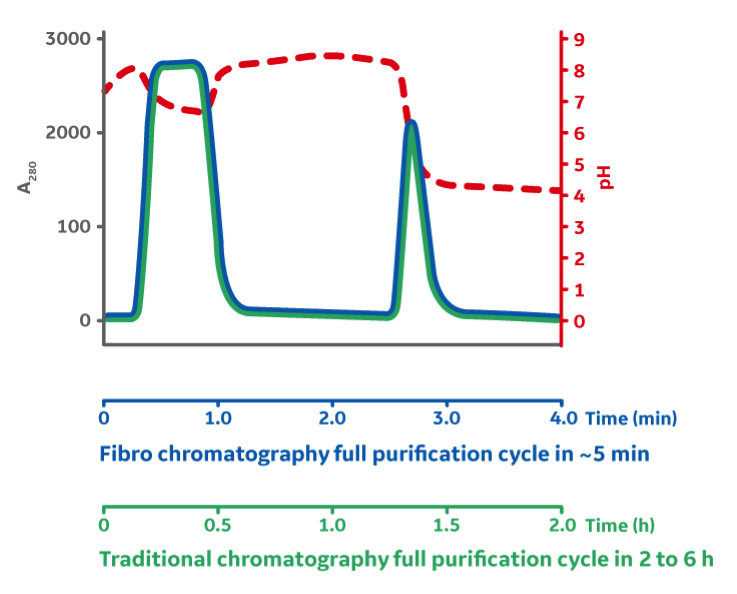
Improved Productivity
The high flow rates and high binding capacities enable either decreased process times or using rapid cycling to decrease fiber adsorbent volume required. Both of these options result in up to a 20-fold increase in productivity compared to resin-based chromatography. Fibro technology permits up to 500 grams of mAb to be purified per liter of adsorbent per hour. In contrast, resin-based chromatography typically generates approximately 25 grams per liter per hour.
Increased Throughput for Research and Process Development Applications
Research and process development typically involves the screening of a large number of clones and cell culture conditions. Frequently, purified proteins of interest are an important part of deciding whether the clone or cell culture conditions tested deliver the protein desired. Fibro’s shortened cycle times can significantly reduce process development time compared to conventional chromatography columns, PreDictor™ RoboColumn™ (Figure 5).
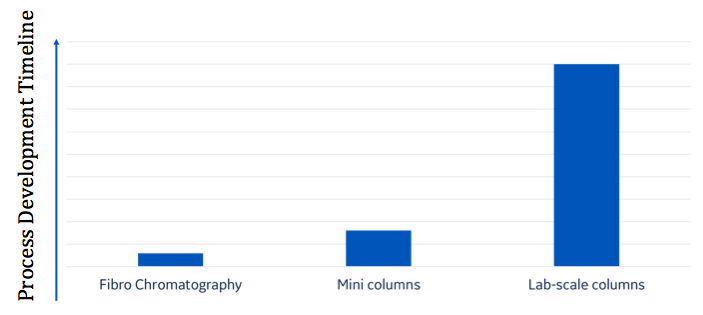
Adapted from: Adams et al. Optimization of a micro-scale, high throughput process development tool and the demonstration of comparable process performance and product quality with biopharmaceutical manufacturing processes. J. Chrom. A, 1506, 73–81 (2017).
Improved Flexibility and Quick Changeover Time
In clinical and commercial manufacturing the rapid cycling enables full unit utilization in a single batch. This will enable cost effective single-use operations eliminating lengthy change over times in commercial manufacturing. This is particularly important in multiproduct facilities resulting in better facility utilization and more batches to be produced.
In Summary
The recently launched HiTrap™, Fibro PrismA™, and HiScreen Fibro PrismA™ chromatography units enable rapid purification cycles in minutes rather than hours as compared to resin-based chromatography. This enables up to 20 times increased throughput in research and process development applications. In clinical and commercial manufacturing, the rapid cycling permits single-use operations that are perfectly designed for single-use equipment facilities, at small to medium processing scale (primarily up to 2000-liter bioreactor volume) and for multiproduct facilities where short turnover times are required or for applications where very fast mAb purification is desired.
For more information, please see Fibro technology