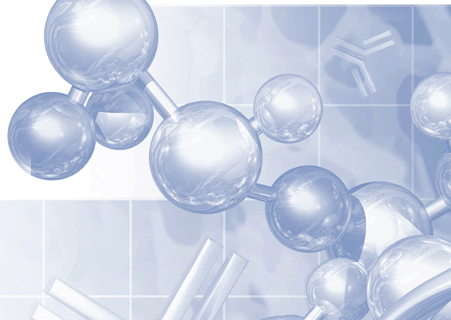
A Guide for Selecting the Correct Filter Integrity Test Instrument
Overview
Selecting the right filter integrity test instrument is an important task. An informed, balanced choice will support the seamless integration of the instrument into critical processes and provide trouble-free operation for years to come. The right choice may be made more difficult by different departments, or user groups, who may assign a different value to the same feature. A rational approach is beneficial to ensure the selected instrument can fulfill all the selection criteria for all interested parties, with any compromises being limited to non-critical characteristics.
The critical features of an integrity test instrument can be very different, depending on whether it will be used independently to produce paper documentation for inclusion in paper batch records, linked to a network to produce electronic records, or be remotely controlled using process control equipment.
In this guide, we have outlined a helpful set of criteria to help you compare and evaluate the features of the best-in-class integrity test instruments and to make informed choices. We have also highlighted helpful tips for working with suppliers to ensure you collect all the information you need to make the best decision.
Core Requirements
Design
Ease of Use
Ease of use is often cited by operators as the primary factor that affects their selection of an instrument. This is a significant aspect to consider when deciding on the right choice for any application. Instruments that are easy to use also tend to be quick to learn, quick to adopt, and reduce deviations by minimizing operator errors. Easy to use instruments also simplify the training and routine re-training burdens demanded in any GMP process, saving operator time and reducing training costs.
Environment of Use
Integrity test instruments may be used in a wide variety of environments ranging from uncontrolled plant areas to highly controlled and monitored cleanrooms. The physical design of the instrument should be suitable for each of the environments that it may be used within. Best in class instruments will have design features to support the use in clean environments. These features may include an absence of internal ventilation that may generate particles or simply being dust and splash proof, perhaps with appropriate IP ratings that support the external cleaning requirements common in these most challenging environments.
Reliability
Most integrity test instruments are exposed to liquids and aerosols that might contaminate their internal components. If not managed properly, that may lead to increased service costs, or cause a loss of function or accuracy of the instrument over time.
Best-in-class equipment will have methods to avoid process liquids draining back into the instrument and may also utilize an internal diagnosis program to check the critical hardware performance at regular intervals. This is executed to highlight any potential issues before using the instrument in critical tests.
Function
Supported Tests
In certain environments, some instruments could be better suited to particular types of integrity test than others. In general, there are three types of filter integrity test: forward flow (diffusive flow), bubble point and water intrusion.
Best-in-class instruments may also allow for the application of the same measuring technology to other pneumatic tests such as leak testing of various fixed volume vessels or systems and the installation testing of single-use systems. Additional functionality may provide further opportunities to control future process risks with no further investment.
Accuracy
As the accuracy of any instrument increases, the process risk resulting from the potential for a filter integrity test providing a false result decreases. Both false passes and false failures impact upon either the process safety or efficiency, and are highly undesirable.
The claimed accuracy of the integrity test instrument might vary from 3% to as much as 10%, for different measurement ranges.
Underpinning the accuracy claim of any instrument are its calibration methods. Should you wish to confirm those claims, comparisons can be performed using gas flow measurement references that are typically available from 1 mL/min to 1000 mL/min. They can be used to confirm the performance for diffusive flow testing. No equivalent references exist for the measurement of the bubble point, therefore a claim for accuracy based on reproducible measurements cannot be given.
Speed
Some flow measurement technologies, when coupled with validated algorithms, may be able to shorten the filter test times without any compromise of the measurement accuracy. Shorter test times release valuable resources for other process tasks and speed the progress of process operations.
For users that need to test large numbers of filters, even more time can be saved by using instruments and extensions that can support the testing of multiple filters without the operator returning to the instrument during the testing.
Compliance
Validation
According to GAMP5 guidelines, integrity test instruments are typically rated as software category 3 and hardware category 1. Additionally they can be defined as an ‘off the shelf’ instrument. For such instruments a comprehensive validation/qualification package prepared by the vendor can reduce the qualification efforts for the user significantly.
Calibration
Regular calibration of instrumentation is an integral part of GMP compliance. However, it can be easily overlooked when focusing on the design and function characteristics of an integrity test instrument.
Best-in-class instruments should be supported by first-class service. It is much more convenient for calibration and service to be performed onsite, as shipping instruments can incur avoidable delays and costs.
Data Safety and Transfer
For electronic records, the instrument needs to offer the controls for use in environments subject to 21 CFR Part 11 regulations on electronic signatures and records. Some of the controls required for these purposes should be validated on the instrument.
There must be an option to create a backup of the electronic test results and to store them in a safe place. It also ought to be possible to test for data integrity on the backup file.
After-Sales Service, Support and Training
Best-in-class instruments are generally supported by excellent customer service to assist with the use of the instrument throughout its service life.
Automation
Protocols
Some integrity test instruments might be integrated into automated process control equipment and can even be remotely controlled. If you consider this option, it is important that your chosen instrument offers an automation protocol that works for you.
Customization
Your process can have very specific requirements and you may not find the perfect integrity test solution for your process from any supplier on first review. Some manufacturers are able to provide tailored solutions to meet your unique needs.
Third-Party References
Obtain references and published reports describing the instruments. Seek out other users in your company (perhaps in a different location), who have experience that they can share.
By taking all of the above criteria into account and getting feedback from other users, you will be on the right track to choose the best filter integrity test instrument for your process.