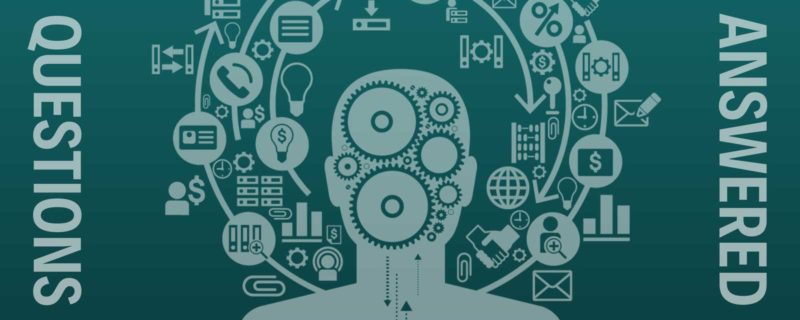
Evaluating Plastic Film for Single-Use Technologies in Biomanufacturing
We recently finished our Ask the Expert discussion on Considerations in evaluating new plastic film for single-use technologies and film development. During this Ask the Expert session, we discussed film selection topics including partnering with suppliers to select and develop industry applicable films, leak resistance, shelf life, films for vaccine manufacturing, and films when lipids are present in media. Other topics included extractables and leachables testing, risk assessments, scaling up or transitioning to single use, film standardization.
Plastic Film for Single-Use Technologies
The increase in adoption of single-use bioprocess technology for manufacturing biopharmaceuticals has been driven by the many advantages it offers, such as increased flexibility. However, the materials of construction can be more complex than conventional stainless steel vessels. Single-use containers are constructed from plastic films, which are often composed of several layers of polymers with additives for processing and performance.
The diversity of applications for single-use containers requires film that can achieve a wide variety of performance attributes such as mechanical strength, flexibility, biocompatibility, and suitable gas barrier properties to name but a few. The right balance of chemical composition and film architecture is critical for achieving desired performance across many applications. Also, in light of industry reports of a leachate, originating from bioprocess containers, that can negatively impact cell culture growth with certain sensitive cell lines, it has become imperative to understand the profile of extractable compounds resulting from the film chemistry. Over the past several years, GE Healthcare has worked closely with biopharmaceutical manufacturers to understand their applications and resulting requirements for bioprocess film performance. This investment in learning has led to the establishment of a scientifically driven film development process focused on the innovation of bioprocess films that are fit for purpose. The process is built on a strong foundation of knowledge in science, engineering, and bioprocess applications and incorporates key learnings about extractables and leachables, as well as considerations for security of supply via supply chain management.
This session was sponsored by GE Healthcare and hosted by Susan Burke. Dr. Burke joined GE Healthcare in 2015 in the role of Material Science Leader in BioProcess R&D. She holds a Ph.D. in Materials Chemistry from McGill University and has expertise in polymer technologies for healthcare applications. Prior to joining GE Healthcare, she spent more than ten years in various R&D roles within the pharmaceutical and medical device industries overseeing product and process development initiatives.
To learn more about plastic film for single-use technologies, please attend Dr. Burke’s presentation at BPI West:
Technical Considerations in Developing a New Plastic Film for Single-Use Technologies
Susan Burke, PhD, Material Science Leader, BioProcess R&D, GE Healthcare
Below is a sneak peek of the discussion, for a full transcript, please see – Ask the Expert – Considerations in evaluating new plastic film for single-use technologies and film development.
What are the important factors to consider when evaluating film for single-use applications?
The Answer:
Defining the critical to quality attributes needed in single-use applications is the first important consideration. Once those are established, an in depth understanding of the materials of construction is needed in order to be able to make the right selection of materials. This includes knowledge about the physical and mechanical attributes, as well as the chemical structures and degradation profiles.
What about leak resistance? As you have made changes to reduce leachables how has this impacted the strength of the bags?
The Answer:
In order to ensure a film will have optimal strength for bioprocess applications, the polymer resins and additives must be carefully selected and optimized. A combination of chemistry, biology, and engineering design factors must be considered to achieve the critical to quality attributes of a bioprocess film.
In the case of Bioclear™11, specifically designed for Wave™ Bioreactors, the concentration of the antioxidant tris(2,4-di-tert-butylphenyl)phosphite) was lowered to reduce the level of extractables. However, extensive testing was done to confirm the reduction in antioxidant concentration did not impact the form, fit, or function of the film. The physical properties of the film, such as tensile strength and modulus, are unchanged. For more details about the comparability study of our Bioclear™ films, click the link below.
Film selection for bioprocess applications requires consideration of how the design of the film influences the chemical, biological, and engineering performance attributes. At GE Healthcare, through collaboration with our Global Research Centers, we draw upon our strong foundation of material science knowledge and combine it with our understanding of bioprocess application to advance our scientific acumen in film development.
We are a lab scaling up from benchtop glass bioreactors to disposable bags, but are still working at fairly small scale. What kind of film questions should we be asking as we make the transition?
The Answer:
Selecting a single-use assembly for an intended application requires consideration of a number of factors. For example, operating parameters such as temperature, humidity, working volume, and run time are key inputs. In addition, knowledge about the sensitivity of a particular system to the ingress of gases (O2 or CO2), loss of water, or shifts in pH must also be factored into the selection process. Evaluating these inputs in comparison to the performance attributes of a single-use assembly can help determine the suitability of the system for the specific application. Some of the key performance attributes of single-use assemblies include tensile properties, biocompatibility, gas barrier properties, extractables profile, puncture resistance, operating temperature range, chemical compatibility, and film clarity to name but a few. At GE Healthcare, we have advanced our scientific evaluation of films, combining the chemical and physical attribute testing with cell culture growth performance. Our systems have been implemented into many cell culture and fermentation processes. In addition, we partner with customers to understand their applications to help us provide solutions for their performance demands.