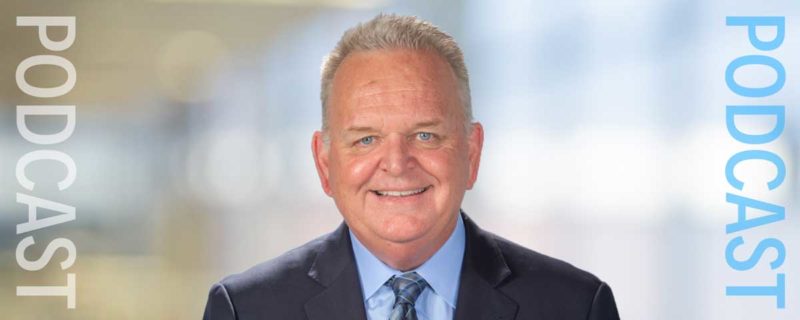
Evolving Beyond the Status Quo with Next Generation Buffer Prep Solutions
Podcast: Download (Duration: 14:02 — 11.2MB)
Subscribe: Apple Podcasts | TuneIn | Deezer | RSS | More
In this podcast, we spoke with Chris Rombach, Vice President of Sales and Marketing at Asahi Kasei Bioprocess America about buffer prep and delivery systems. We discussed current pain points and how next generation buffer prep solutions can greatly improve upon the status quo, including increasing the use of automation and remote operation, while reducing the overall footprint, labor and cost associated with more traditional approaches.
Buffer Preparation – Source of bottleneck and pain points
We began the interview by discussing how buffer preparation is frequently seen as a challenging aspect of downstream processing and the source of bottlenecks. I asked Mr. Rombach why buffer preparation creates the potential for so many issues in downstream. He explained that there are several challenges regarding buffer preparation, primarily, the space that it requires, both from a physical and environmental perspective. The space also needs to be well segregated to eliminate contamination concerns from fugitive emissions during powder dispensing. He went on to say that another issue is the sheer number of different buffers that need to be used in a campaign, which require significant storage space, prep time, and material handling.
I then asked about the most pressing pain points in biomanufacturing. He shared that first, buffer prep is a low value-add activity, but it has substantial impact on facility design, maintenance, and human resources. It is a challenge to be able to coordinate having all the right buffers available on demand.
In addition, powder inhalation and exposure are a growing concern for the operators. The current techniques are still fairly rudimentary and they do not address ergonomics in many cases. Most importantly, you must have a segregated facility with a dedicated space for weighing and dispensing of the powders, hydrating, and blending.
Buffer Preparation – Process improvements
We then discussed how buffer preparation methods have stayed rather static for many years, maybe because of the perception that buffer prep is low value add. Recently however, there has been a shift toward improving the process. I asked Mr. Rombach to explain process improvements like inline buffer formulation and how it compares with inline buffer dilution.
He explained that inline buffer formulation differs from inline buffer dilution in that buffer formulation allows you to create complex buffer solutions, some with as many as 6 to 7 constituents, and this is done via precise flow control, pH, and conductivity measurement. Buffer dilution, on the other hand, is simply the volumetric dilution of a single constituent with a solvent, most typically water. Inline buffer formulation results in a much more precise output, particularly if there are slight variables in the input materials.
For example, if your concentrate solution changes from a 3 molar solution to a more concentrated formula solution, the machine can auto tune itself to provide the desired output based on a well-defined finished product specification and real time measurement of key parameters, namely pH and conductivity.
Inline Buffer Formulation
I then asked how an inline buffer formulation approach can address the common challenges we discussed earlier. He stated that it has the potential to significantly reduce the number of inputs that you use relative to their concentration because it can detect the level of concentrate that is coming to the machine and make sure that it meets the specification requirements. Secondly, the real time monitoring assures product consistency from batch to batch and therefore eliminates much of the typical testing and manipulation of a handmade batch. Finally, by using concentrated raw materials and formulating on the fly, the customer can significantly reduce the footprint in their buffer prep area. Moving to a premade concentration with an inline buffer formulation skid also eliminates the need for segregation of powder handling by eliminating dust emissions.
I followed up by asking him to describe the MOTIV™ inline buffer formulation system. He explained that MOTIV is the new name for Asahi Kasei’s existing line of buffer formulation skids, which have been manufactured since 2012. The systems have all been designed with the user in mind. They are very small and compact, with standard three and five pump systems. Each are wheeled consoles that fit through a standard doorway. Even the largest systems have the smallest footprints on the market. They can be connected to either single use bags or traditional tanks, which can really improve manufacturing efficiency because less liquid needs to be stored. Lastly MOTIV systems integrate nicely into customers’ data collection systems, improving record keeping and traceability batch to batch in a 21 CFR compliant environment.
He went on to describe the different available MOTIV models. He said that there are three different models with the key difference being the number of inlet pumps on board as that relates to the number of inlet solutions the operator can use. The MOTIV 3 is the simplest model with three inlet pumps, one of those is typically used for concentrate, the other for pH adjustment, and the third for Water For Injection (WFI). For the MOTIV 5, it has five inlets that are designed to handle more complicated formulations, yet still in a standard package. Finally, MOTIV 5 plus offers a fully customizable design. MOTIV 5 plus systems have been designed with as many as seven inlet pumps flowing up to 15,000 liters per hour. All MOTIV models come with an Ocelot automation platform, are 21 CFR compliant, and support wide pump turn downs to create a wider set of finished products.
Increasing Buffer Prep Efficiency
We then discussed how large volume and multiple buffers could be handled more efficiently. Mr. Rombach described how for extremely large volumes, buffer formulation can play a crucial role and can be a game changer in facility design. He went on to provide an example, where one of their customers was investigating making a sodium chloride solution by hydrating and mixing crystalline sodium chloride during their facility design phase. They realized that the sheer volume of solids and therefore super sacks of salt that they would have to handle daily was almost insurmountable. They elected to have a concentrated solution delivered via tanker and then formulate and dilute from there to best handle multiple buffers. He stated that Asahi Kasei works very closely with their customers to evaluate the extensive list of buffers that they must prepare. From there, they can make recommendations about the appropriate sequence in which the buffers are made. This increases a customer’s speed, minimizes their cleaning and rinsing, while still assuring adherence to final product specs.
I then asked about another area of concern, the space required to meet buffer demand and how footprint could be reduced. Chris explained that by the very nature of its design process, buffers are now being made in an on-demand manner rather than in bulk and stored for periods. By working with concentrates, multiple final products can be produced from a handful of starting ingredients, thus reducing the need for storage. For example, if you are using a 5X concentrate and blending as needed, you can potentially reduce your storage requirements by that same factor. Additionally, if a biologic manufacturer partners with a liquid concentrate provider, they can eliminate, or at least greatly reduce the amount of space required for storing, weighing, and packing of powders, an effort which traditionally consumes a lot of space, requires protective gear for the employee, dedicated air handling, equipment, and extensive labor.
Automating Buffer Prep
We moved on to talk about the shift toward increased automation and remote operation. I asked Mr. Rombach how automation and remote operation are incorporated into the MOTIV systems. He explained that all of the MOTIV systems come with the ability to automatically perform autonomously in a 21 CFR compliant platform. The Ocelot automation platform allows the user to create batching schedules to carry out sequential batch manufacturing over a prescribed time, all independently. They have also designed Ocelot for an OPC environment, thereby allowing the machine to be connected to customers plant wide and this assures the ability to remotely control, monitor and collect data in a singular plant wide approach. Another remote operation feature is the browser-based method editor that allows an administrator to add new formulations into the system. Even while it is running from any PC that is connected to the internal network, this intuitive interface simplifies method creation and editing with the capability of performing the steps from the comfort of their office. It is possible to work on the machine itself, but the ease of being able to administer changes from the desktop is a really enabling feature for the user.
Closing Thoughts
I closed the interview by asking Mr. Rombach if he had anything else to add for listeners. He said that the biggest thing is that manufacturers have looked at other aspects of operation that seem to be more important or sophisticated. As a result, people have been lulled into complacency because of the ease of making buffers. But when you step back and you look at what is the best way to design a facility, incorporate faster operations, reduce storage volumes, have an open ballroom suite type processing area working with liquid concentrates, and formulate on the fly, buffer prep is a big part of that. With automated buffer prep solutions, facilities do not need a segregated dispense area or separate batching and compounding areas. Therefore, buffer prep is an area that a good manufacturer should be really looking at and scrutinizing, because they could realize tremendous gains in productivity and reductions in costs while delivering a more consistent final product. The entire system that is required to supply especially large volumes of buffer is more complex and is an area ripe for improvement.