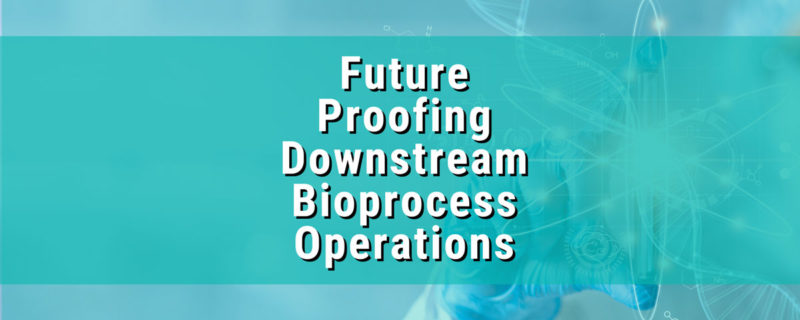
Future Proofing Downstream Bioprocess Operations
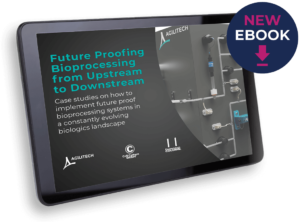
“ Future proofing Bioprocessing from Upstream to Downstream”.
You can download all the articles in the series, by downloading the eBook.
Historically, downstream bioprocesses have been simpler than upstream bioprocesses. They were more manual and Protein A columns permitted a simple and effective purification solution for monoclonal antibodies and protein-based therapeutics. More recently, upstream bioprocesses have undergone significant improvements in process and subsequently yield. These improvements in upstream created bottlenecks in downstream as the systems in place were not prepared to adjust to changes in both the starting material from upstream and yield. As a result, downstream bioprocesses have had to evolve to meet the needs of these new challenges by incorporating technology advancements such as single-use technologies, improved chromatography solutions, continuous processing, advanced buffer management systems, increased automation, and many others.
The future of downstream bioprocessing will require additional improvements and the industry will need to stay aware of changes in upstream bioprocessing that will have an impact on downstream bioprocessing. While it is not always possible to anticipate every need in advance, the goal should be to design downstream systems that are flexible and can be adapted to meet the needs of future advancements and challenges. Part of the solution is ensuring that systems are fit for purpose to begin with and then from there are easily reconfigurable, allowing the workflow to evolve and integrate beneficial new technologies.
In this article, we look at some examples of how downstream bioprocessing solutions can be designed for flexibility, fit for purpose, and to be future proof.
A Workflow That Can Evolve
It is important when designing solutions for now that companies also consider future needs such as changing process requirements, scalability, and potential improvements. Future proofing a manufacturing system requires a good understanding of both short- and long-term goals for the process as well as current issues that need to be resolved. With forward looking planning and design, companies can purchase only what they need currently, but with the supports in place to adjust the system as needed.
Case Study – Future Proofing by Solving Current Problems while Considering Future Needs
In this example, Agilitech met with a client that was running their current process through a hollow fiber TFF filter for microfiltration, but because the starting material was so viscous, they could not use dead end filtration. Instead, they were using tangential flow filtration, which allowed them to ease the material through the system.
To future proof their system and allow them to process more material with the same unit, Agilitech created a custom skid that could run one or two hollow fiber filters in parallel. The company’s current needs and processing material only required one filter, but they anticipated their volume increasing and wanted to be able to run faster outputs or larger volumes without increasing the overall processing time. Agilitech configured a system that could support a second filter in parallel to address future increases in volume. With this solution, they would be able to easily make the changes themselves by just installing the appropriate tube set and changing some parameters. These features ensured that the company could future proof their system to be able to grow and adapt to the specific process requirements for their five-year production target.
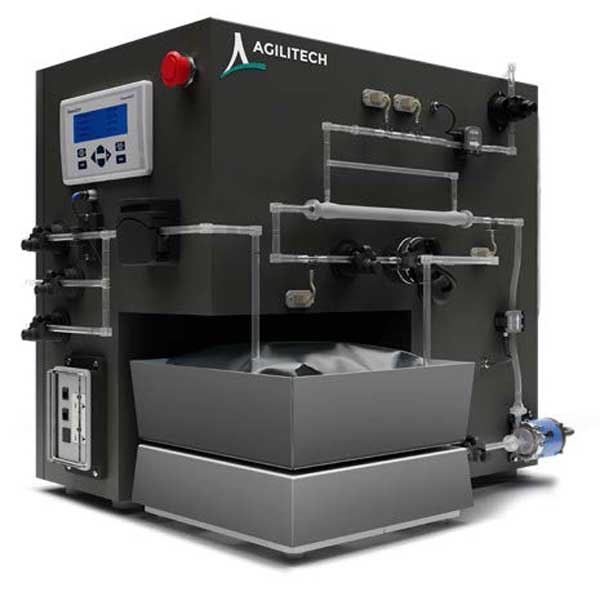
Agilitech tangential flow filtration (TFF) systems range from benchtop size to up to 100 LPM and feature a unique brand-agnostic design that can be tailored to meet a customer’s specific needs. The fit-for-purpose design offers options and possibilities for every facet of the system including preferred brand filter and customizable bags, to the automation and control platform.
Managing Supply Chain Delays
Supply chain delays are plaguing the industry right now resulting in significant equipment and raw material shortages, largely due to the impact of the COVID-19 pandemic, but also due to an increase in single-use product demand¹ Some of these materials are prone to shortage; this includes some key high-purity polymers.² As a result, end users can face long delivery times for certain equipment and consumables.³
A more open or agnostic approach to equipment brands can address supply challenges by permitting more flexibility when sourcing products from vendors. This allows customers to search for the quickest delivery and best pricing across a range of products and vendors rather than being tied to one specific solution.
Agilitech’s approach is to provide brand-agnostic systems that can be reconfigured to use components from different manufacturer brands. As a result, Agilitech is not limited to the same supply chain constraints that other vendors are; if there is an issue with delivery of a specific component, they create a custom solution or can move to a different vendor with quicker delivery times without any effect on the design or the delivery of the system.
Case Study – Avoiding Supply Chain Delays with a Custom Brand-agnostic Approach
Agilitech worked with a customer that had a specific need that could not be addressed in a timely manner by ordering from another vendor due to supply chain demands and lack of availability. The customer was using a production scale single-use chromatography skid from a different supplier. They wanted to add a lab scale size single-use chromatography skid that would match as closely as possible their current production size skid. However, when they purchased a lab scale skid from a different vendor, they found out that it would be a month or two for delivery and that the new skid was not single use. This made the new system very different from the one used in manufacturing and resulted in the need for a custom solution in order to be as close as possible between process development and manufacturing.
They asked Agilitech to create a custom single-use chromatography skid to match their production size skid. Agilitech was able to complement the configuration of the other supplier’s production skid. This enabled the company to do process development, testing, and other studies at lab scale while matching the same configuration of their production scale version.
Obtaining Exactly What You Need with Fit-for-purpose Solutions
Market-leading suppliers offer a range of platform systems with some flexibility within their platform of products. However, full flexibility of these products can be limited as the equipment itself is not always adaptive to unique process needs and typically do not integrate products and/or components outside of brand. Typical industry practice is to reconfigure these standard systems on the back end to meet specific process needs. However, this approach is typically less effective and ends up costing more.
The industry needs more flexible solutions that can be tailored to specific bioprocessing needs, as well as solutions that can adapt and evolve as process requirements change. Agilitech uses careful front-end planning and flexible design to provide customers with a true fit-for-purpose solution that is tailored to their unique process and that can be adapted as that process evolves.
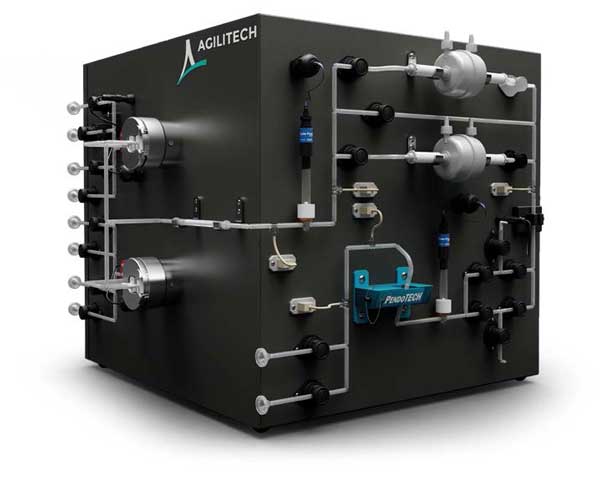
With an open system design, Agilitech’s single-use chromatography systems provide flexibility to choose preferred brand of column, filters, and other components, as well as the automation and control platform. The chromatography skid is engineered to accommodate optimized column sizes and resin quantities to meet specific process needs and to keep raw material costs as low as possible.
Case Study – A Very Specialized Solution for a Unique Request
In this example, Agilitech worked with a customer that had a number of unique needs for their system. They needed a tangential flow filtration system that could adapt to flat sheet cassettes, 12-inch hollow fiber filters and 24-inch hollow fiber filters. The system had to be capable of handling those very different kinds of filters while maintaining usability and not increasing hold up volumes.
Agilitech knew that they needed to design to accommodate every scale, so that when the client was using the smallest scale filters the system was not cumbersome because it was oversized. Agilitech developed a way to put certain components on a single frame and made the frame movable within the skid boundary, so certain equipment could be moved to where it needed to be to make it most optimized for that configuration. With this skid configuration, the customer could move the permeate and the retentate instruments and valves to a specific position for optimal use for that configuration. This was achieved using linear actuators, so it is also automated. The linear actuators move with a motor that uses predefined set points to move into a specific location.
Case study – A Perfect Design to Address Potential Supply Chain Issues, Future Needs and a Truly Fit-for-Purpose Solution
In this case study, Agilitech worked with a client that is a leader in the discovery and production of enzymes for molecular biology applications. The customer needed a new tangential flow filtration (TFF) system to support production of electrocompetent cells. Their production process depended on accurate tangential flow filtration, an essential step for washing their material before preparing the product for market. The company had outgrown its current TFF system as demand for the product increased. Higher volumes required the client to run their system weekly as opposed to bi-monthly to keep up with production. Frequent processing runs meant increased costs for disposables that were becoming more and more difficult to procure due to supply chain constraints. Furthermore, as a company producing another 400 products, the frequency of running the system was interfering with the production of other biologics. The company was searching for an engineering solution that would maximize their throughput while easing workflow processes to future-proof production.
Agilitech was able to solve their problem by designing a TFF system specifically to meet the company’s needs. Simultaneously, Agilitech examined the company’s process to identify the core problem. Agilitech found that the company was using a TFF system that was designed for flat sheet cassettes, whereas the client was using a 41-inch hollow fiber filter. As a result, the company was experiencing problems in their process, specifically high pressure along the filter, which forced them to slow down the flow rate, resulting in extended processing times. Their initial system worked with a 20 L bioreactor that would yield 2 L of concentrate in approximately 6-8 hours. With future goals to double throughput, eventually working with a 40 L bioreactor to yield 4 L of concentrate, the company wanted to ensure faster production times. Additionally, there were problems with accuracy in the diafiltration process. The nature of the company’s product meant they were working in microsiemens, but the sensor of their diafiltration skid was scaled to millisiemens for conductivity. This made it difficult to determine when the diafiltration was complete and was impacting their product volumes as they took off samples to confirm their results.
The solution required Agilitech to investigate filter options with WaterSep Bioseparations Corp, the hollow fiber manufacturer that was supplying the company with their filters. Agilitech determined that a 24-inch hollow fiber filter would be more effective than the original 41-inch filter; its wider diameter would provide more surface area and channels for improved processing. Where the client originally sought a solution for adjusting their TFF system to handle a small filter, Agilitech understood that the problem was about upsizing the filter.
Keeping in mind the client’s priority to future-proof their system, Agilitech also provided them with a pump that could handle flow rate requirements for multiple size filters, to allow for future upsizing. The result, Agilitech adapted its standard TFF system to allow for much higher flow rates, at high pressures, without stressing the system. Agilitech and its customer are expecting much higher throughput volumes, and faster concentration and diafilitration processes. Whereas the customer’s original TFF system was running 800 mL/min in feed flow across the filter, the Agilitech system sets a new target of 19 L/min for a cross flow rate. Adjusted for degradation of flow based on cell material, Agilitech still estimates cross flow within the 5-10 L/min range.
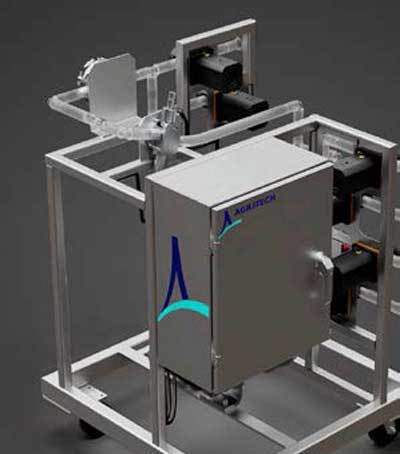
The Agilitech inline dilution system automates buffer preparation and delivery to overcome bottlenecks and improve downstream bioprocess efficiency by eliminating manual labor and buffer storage capacity issues. Fit-for-purpose options allow the system to be adapted with additional inlets and pumps and the brand-agnostic system design enables use with preferred automation and control system.
The Agilitech TFF system not only allows the customer to reach their priority goal of increasing throughput, but also allows for more automation. Agilitech provided a tailored, user-friendly operating system that can be easily transferred to an operator, freeing up the time of the company’s lead expert.
What’s more, Agilitech’s brand-agnostic engineering solutions have the additional benefit of allowing the company to order single-use components from different suppliers, an essential design feature to ensure agility in the face of potential future supply chain problems.
Conclusion
These types of process problems are somewhat typical for the biotech industry. Many of the single-use technologies currently on the market offer some degree of customization; however, there are typically limits to how much the solution can be tailored to the specific needs of the customer. Biologics manufacturers often must fit their process to the available technologies instead of the technology meeting their exact needs, often resulting in a technology solution that is sub-optimal for the process. Companies seeking to customize their systems to fit their process also find themselves piecemealing different components to achieve their production goals. When problems arise, they face resistance from their supplier’s support teams as they have used equipment in non-standard ways. For Agilitech, the engineering challenge with this customer was about not only designing a fit-for-purpose solution that was exactly what the client needed, but also about reframing the problem.
It is important for customers to remember that there are companies who can engineer a true best fit solution. Don’t be afraid to ask for an engineering challenge that might initially seem daunting.
Footnotes
-
1. Sanders, P. (September 21, 2021). Future-proof Bioprocesses: Flexible Single-use Technology that Adapts to an Evolving Industry. Accessed September 1, 2022 : Retrieved from https://downstreamcolumn.com/future-proof-bioprocesses-flexible-single-use-technology-adapts-evolving-industry/.
-
2. Rader RA, Langer ES, Jhamb K. COVID-19 Impact on Bioprocessing: Accelerating Trends and Long-Term Impact of Novel Coronavirus-19 on Biomanufacturing and Bioprocess Supply Chain. BioPlan Associates: Rockville, MD, June 2020; https://bioplanassociates. com/wp-content/uploads/2020/07/Covid-19-Impact-on-Bioprocessing-White-Paper-BioPlan-20200605.pdf.
-
3. Sanders, P., & Sargent, B. (Oct. 28, 2021) Addressing the increasing demand for single-use technologies and supply chain shortages with future proof systems. Accessed September 1, 2022 : Retrieved from https://downstreamcolumn.com/addressing-increasing-demand-single-use-technologies-supply-chain-shortages-fu ture-proof-systems/.