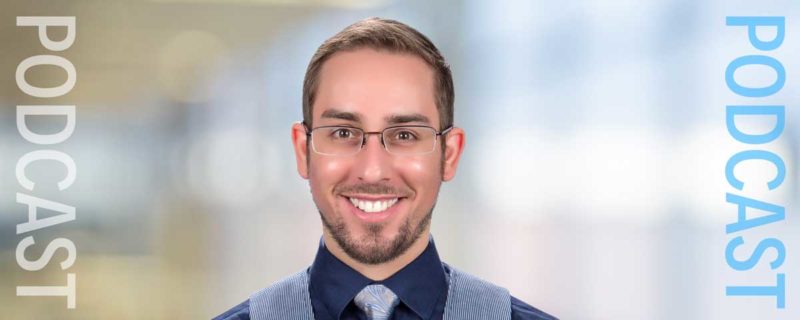
Increasing Liquid Chromatography Efficiency with Fully-controlled Binary Blending
In this podcast, we spoke with Cory Hinz, Engineering Manager at Asahi Kasei Bioprocess about the different methods that are available for liquid chromatography mobile phase solutions and the benefits of inline blending. Cory also describes how to implement binary blending feeding of a liquid chromatography process using inline blending.
Liquid Chromatography Mobile Phase Solutions
I began the discussion by asking Cory if he could tell listeners about the different methods that are available for liquid chromatography mobile phase solutions. He explained that for chromatography, it’s important to remember that the process and the chemistry should drive the method used. Some chromatography processes use prepared mobile phase solutions that don’t require inline mixing, while others blend two or more solutions together to formulate. The mobile phase takes these blends and changes their composition over the course of the elution. Each of these methods is driven by the needs of the process.
Inline Blending
Next, I asked Cory if he could tell us about the benefits of inline blending. He said that inline blending allows solutions to be prepared at their point of use, not just for chromatography processes, but any blending process. This increases the consistency of the blended solution, reduces dependency on the accuracy of raw materials, allows for real time quality assurance, and eliminates the risks and extra resources and space required for traditional tank approaches. Inline blending also adds an element of flexibility, allowing functions such as buffer preparation to become more of a utility than an additional process.
Binary Blending Feeding of a Liquid Chromatography Process using Inline Blending
Cory then provided details about how to implement a specific solution for binary blending feeding of a liquid chromatography process using inline blending. He explained that binary blending is the most common configuration they see for their chromatography equipment customers, because medium and high-pressure liquid chromatography require a dedicated pump to supply the pressure dictated by the process. It is important to design the binary blending at the suction side of the pump. This is done by employing two modulating control valves, one for each of the two components of the mobile phase, and ensuring sufficient supply pressure to each one.
He then told us about the role that each of the valves play in creating the ideal blend. He described how the control valves do most of the heavy lifting for binary blending. The first valve controls the diluent, which will be the purified water or buffer that comprises the majority of the mobile phase blend. The second valve controls the component that is getting diluted. These valves each react to a different process parameter to achieve high accuracy.
The second valve is the most intuitive, the component being diluted can have its proportion increase or decrease based on the movement of the control valve. For example, if the concentrate is below target, the valve will open to allow more concentrate through. This can be based on flow connectivity or any critical process parameter that can be measured inline.
The first valve is less intuitive. It is controlled by the pressure in the system after the two streams have combined. If the blending pressure is too low, for example, the valve will open to increase that pressure.
The result of this configuration is that if the two valves react to one another via the process but are not linked by a system control algorithm. This results in flexibility and accuracy and also provides a way to monitor and mitigate pump cavitation.
Next I asked Cory about controlling the incoming process pressures of each of the valves. He said that in order for the binary blending scheme to work optimally, the incoming supply pressures of each stream should be controlled to prevent fluctuation that can disrupt the automatic blending control. To accomplish this, they employ a booster module on each of the two inlet streams. They have found that this additional feature is successful in isolating the system from fluctuations in supply, due to facility or other environmental effects. He went on to say that it is also convenient to match the two supply pressures to one another because that creates an identical pressure drop over both belts and a more intuitive blending scheme.
He then explained how the booster modules work together to maintain pressure. The booster modules are identical and are each composed of a recirculation loop driven by a load pump. Once primed, the load pump runs at a constant speed and directs flow both through the recirculation circuit and to the control valve. By placing an aero augmented back pressure regulator on the recirculation line, we can automatically control the effective pump discharge pressure. This is the supply pressure that each valve sees. The air augmented design of the back pressure regulator means that the system can target the desired pressure set point by modulating the supply air to the regulator.
I closed our session by asking Cory about other formulation challenges that he gets asked about. He said that not all applications require binary blending, some require combinations of three or more components. This makes system control more complex but is a familiar application for Asahi Kasei Bioprocess. They have tackled this several times in liquid chromatography applications, but the most common implementation of multi component blending is for buffer formulation. Their line of MOTIV™ systems is specifically designed to achieve highly accurate multi-component blends using our proprietary Pro-Yield™ technology. Both their chromatography and MOTIV formulation systems operate on their state-of-the-art, industry 4.0 process control software known as OCELOT™ System Control.
LEARN MORE ABOUT AKBA’S BIOPROCESS CHROM SYSTEMS