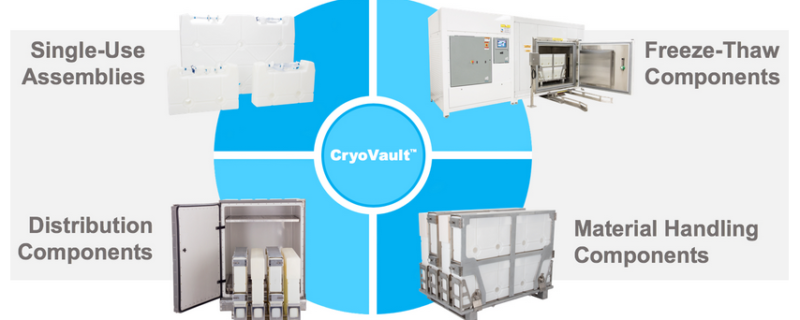
Innovative Single-Use Freeze and Thaw Platform for Bulk Drug Substance
Successful bulk drug substance freeze and thaw is a critical aspect of biologics manufacturing. It is also time consuming and labor intensive. Historically, cryovessels have been the most common technology used for freeze and thaw due to their durability and scalability. However, cryovessels require extensive cleaning processes and infrastructure and labor to maintain them. These challenges, led companies to look for single-use alternatives. While single-use significantly reduces cleaning requirements, they are difficult to scale due to limitations of the size of the bags. Another downside is that they can be prone to integrity issues.
I was pleased to learn about a novel end-to-end, single use freeze and thaw platform, CryoVault™, that incorporates the benefits of a robust, rigid container with the advantages of single-use systems. To learn more, I spoke with Max Blomberg, Executive Director of Operations and Andrew Govea, Senior Product Engineer, at Meissner about the development of CryoVault™ and the written transcript of our interview is included here.
What is CryoVault™?
It is a next generation, single-use freeze/thaw platform, primarily directed at critical high value process fluid such as bulk drug substance. It provides a real change in terms of scalability and robustness compared to current solutions.
What led to the development of the CryoVault™?
Meissner has a history of developing products based on customer need and has been working on a single-use freeze/thaw solution based on customer requests. There was a known industry need for a freeze/thaw solution that was single-use, had increased robustness and was scalable to large volume, particularly with the proliferation of decentralized Drug Substance (DS) and Drug Products (DP) processing sites. Merck came to Meissner with a freeze/thaw product that they had started to develop based on their needs, which happened to be similar to what was driving Meissner’s own development efforts. The Merck team had proof of concept for the product, but needed someone to commercialize it. Meissner vetted the Merck technology very carefully and felt enthusiastic about it and the benefits that it could provide to the industry.
What is currently available for the freeze and thaw of critical biopharmaceuticals?
Historically the use of cryovessels has been the predominant technology. However with recent adoption of single-use systems, new technologies are coming out for freeze thaw that have been imported over from other uses, such as biocontainer assemblies (bag assemblies) with rigid outer support containers. The problem with these is that they have not been designed for the purpose of freeze/thaw applications.
What are the advantages and disadvantages of each of the current options?
The advantage of a cryovessel system is that you can process large batches, around 300 L batch sizes. Downside or areas for improvement are that the cleaning, sterilization, and validation of these systems require extensive infrastructure and labor to maintain. Single-use film based products have all the advantages of single use, but there can be integrity issues because they weren’t designed for freeze/thaw. The films are so thin that they are prone to leaks. Also scalability is a big challenge as it is capped out at 18-20L per system. Large scale bulk drug substance of 300 L or so requires many manipulations. This includes handling operations, not just during freeze and thaw but also in filling, packaging, etc.
How does CryoVault™ compare to these options?
The team at Meissner approached the design of CryoVault™ with a platform system in mind. They looked at the advantages and disadvantages of existing solutions and how freeze/thaw could work best. They then designed the platform specifically around single-use bulk drug substance freeze/thaw. In the design they thought about every step for low temperature application including tubing management & shroud, palatalized load, and container shape to create a comprehensive system. They also had to think through how to test those attributes on a rigid container instead of film. The paradigm shift the product was creating necessitated method development in testing, for example, gas barrier, puncture (ASTM F1306), had to be conducted on a product orders of magnitude more thick than a film. What really attracted Meissner to the product was that it was single-use system for freeze/thaw with all the benefits of single-use and all the features and robustness that you would get with a more traditional rigid cryovessel.
What differentiates CryoVault™ from vessels like carboys, which historically has been another common container for freeze/thaw of BDS?
The key differentiator is the science behind the container design. There was intentional design around how bulk drug substance freezes and thaws. It was important to create consistent freeze path lengths, which is easier to control in a rectangular design than in a circular shape like a carboy. There was a lot of science and engineering that supported the rectangular shape. Controlling the last point of freeze has a direct correlation to container integrity. Consistent freeze path lengths permit scalablity as more BDS can be put into larger containers while freeze/thaw performance remains the same. This provides a faster freeze/thaw cycle, which is critical from an operations perspective. It allows faster freeze times and mitigates cryoconcentration. If BDS doesn’t freeze fast enough then it can compromise fluid integrity and critical properties can change. Another thing that differentiates CryoVault™ is the ecosystem that has been built around the system. This includes specifically designed material handling equipment, the ability to treat this material as a palletized load for increased robustness, a distribution system, and support around the product container.
How has the market received the new technology?
Meissner has been really pleased by the level of interest from the market, which validates their thinking about market need and that it is a unique product. Several clients are testing CryoVault™ and a couple of clients are using it in commercial applications. They realize that this is a unique solution for an obviously critical process step in the customers’ processes and rightly so, there is a high level of vetting by potential users.
Can the containers be recycled or how they are disposed?
This is an area where CryoVault™ really differentiates itself. Most single-use systems have multiple polymers which makes recycling near impossible. CryoVault™ containers are made from a single plastic material, HDPE, which is a very recyclable material accepted by most waste streams. Of course there must be a decontamination step first, but companies can work with their municipalities to explore recycling options.
How can a company get started evaluating the CryoVault™ platform if they were interested?
The best thing to do would be to come to the Meissner corporate headquarters where they have a fully functioning product demonstration suite up and running, to essentially test drive the system. It is a unique technology and it is new, but it is poised well for standardization throughout industry with standard assemblies and aligned surrogate buffers for testing various critical quality attributes at scale in the demo suite. Scalability container samples are available to start the testing process. Companies can talk to Meissner and their team of CryoVault™ experts. There is a whole support group that can answer any questions.
For more information about CryoVault™ please see: