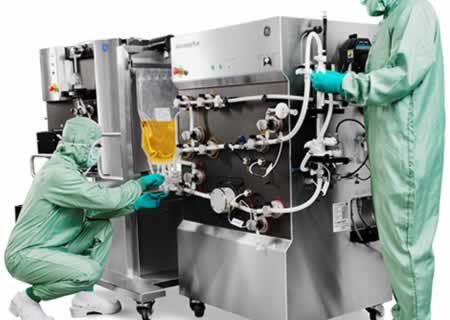
Integrating Downstream Unit Operations – Polishing and Concentration Steps
Most downstream biomanufacturing process steps are conducted as separate unit operations. As such, there are a great number of manual tasks including individual instrument function, intermediate handling of material, and product transfer. This high reliance on manual tasks consumes more resources and introduces greater opportunity for operator error.
Thus, there is a desire to automate and connect process operations to increase process efficiency and accuracy, plus reduce the number of hold steps and process time. While there are many advantages for integrating downstream unit operations, the technologies to integrate these systems have only recently begun to emerge.
In an effort to work toward protocols for integrating downstream unit operations, GE Healthcare recently published an application note, “Connected polishing and concentration under one automation method.” In the application note, authors describe connecting the ÄKTA™ ready chromatography system polishing step to the ÄKTA readyflux filtration system concentration step.
Polishing and Concentration Integration Workflow
Equipment
The ÄKTA ready is a liquid chromatography system built for process scale-up and manufacturing. The ÄKTA readyflux is a TFF system intended for both microfiltration and ultrafiltration applications in both upstream and downstream processes, ranging from pilot to small manufacturing scales. For flexibility and ease-of-use, ÄKTA ready and ÄKTA readyflux operate with single-use flow paths, and both systems are controlled through the UNICORN™ software, eliminating the need for separate automation software. To suit a broad range of applications, ÄKTA readyflux can be used with both hollow fiber filter cartridges and filter cassettes.
Software
The UNICORN software, while providing control for both systems independently, can also facilitate the connecting of these two operations. In the study, GE Healthcare used the software’s Method Queue function and Ready instruction features to connect the two steps. When integrating operations, the Method Queue is used to define which systems are included in the integration as well as the order of individual methods and their initiator. The Ready instruction recognizes when an individual method has been executed on one system and is then used to initiate the start of another individual method on the other system.
Case Study Polishing and Concentration Integration
For the study, GE Healthcare used a process for polishing and concentration of bovine serum albumin (BSA) as a model for the integration. The ÄKTA ready and ÄKTA readyflux were connected to one computer each, both installed with UNICORN software A schematic description of the setup is provided in Figure 1 (courtesy of GE Healthcare). For transfer of the process material, process steps were interconnected via tubing from the ÄKTA ready outlet to the ÄKTA readyflux recirculation bag.
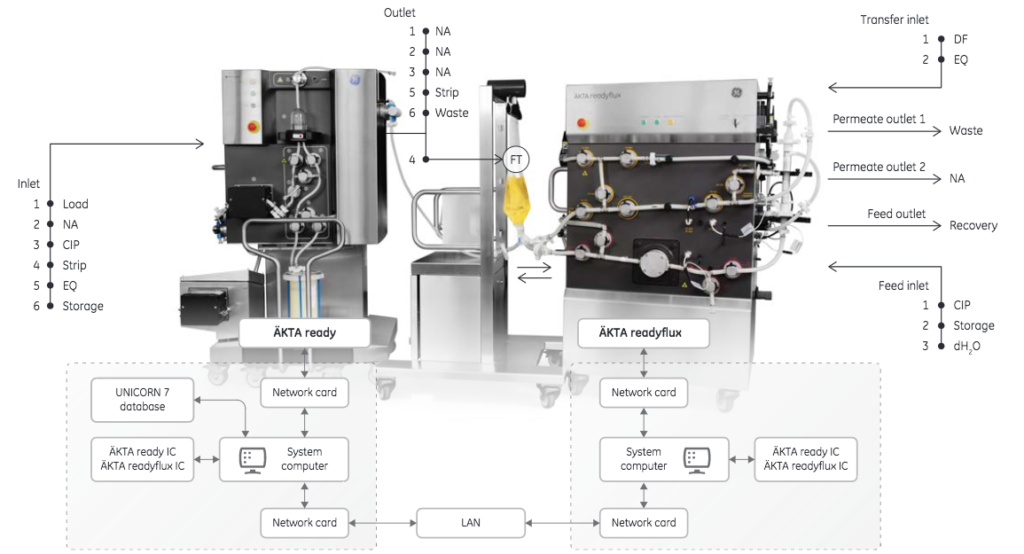
Method Creation
Method creation was executed using method phases predefined in the software. With the ÄKTA ready individual methods were created for column cleaning-in-place (CIP), equilibration, load, strip, and storage. For the ÄKTA readyflux, individual methods created included CIP, equilibration, batch concentration, diafiltration, final concentration, recovery, and storage. A screenshot of the Method Queue for this integration can be seen in Figure 2 (courtesy of GE Healthcare).
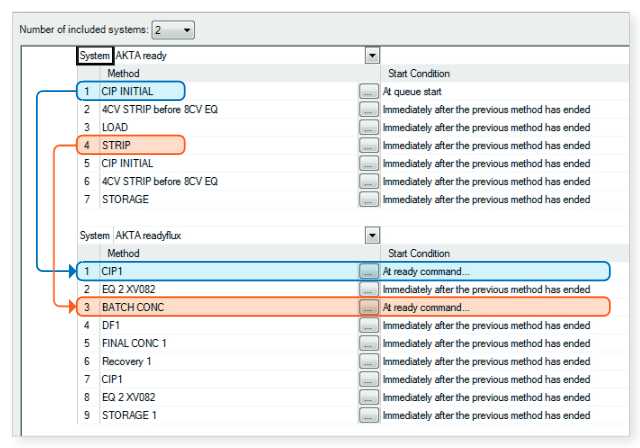
Results
The aim of the study was to determine whether two separate unit operations, in this case polishing and concentration could be integrated using the UNICORN software. It was demonstrated that integration was successfully executed in a consecutive manner using the Method Queue and the Ready instruction functions. Graphs showing execution of the individual methods are presented in Figure 3 (courtesy of GE Healthcare).
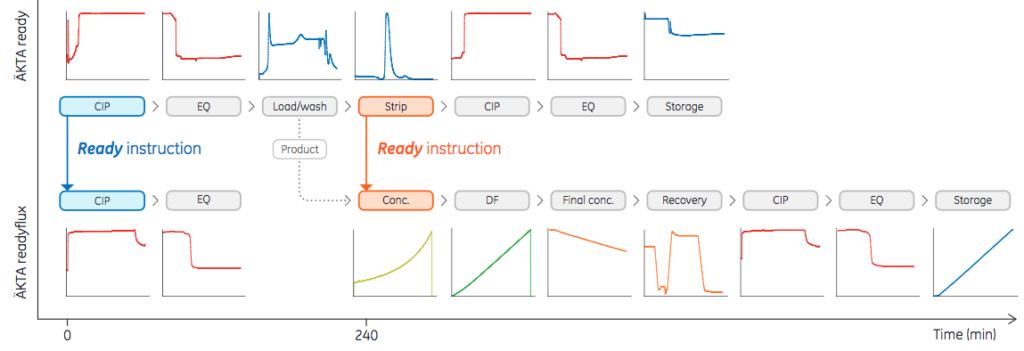
Summary
Integrating downstream unit operations provides many process benefits, including a reduction in the amount of manual operation and resources. The connection of unit operations also minimized intermediate hold steps and provided an overall reduction in process time. Key advantages of using this combination of equipment and software were 1) unit operation can be ran automatically and in parallel saving time 2) the use of single-use flow paths eliminated the need for costly and time-consuming cleaning and cleaning validation.
Authors identify that this integration brought flexibility and speed to process operations and the described solution is especially beneficial for manufacturers operating in smaller scales, with many parallel productions.
For study details and more information on the integration of downstream unit operations, please see Connected polishing and concentration under one automation method
Other related downstream content:
- https://downstreamcolumn.com/automated-single-use-filtration-increase-efficiency-upstream-downstream-operations/
- https://downstreamcolumn.com/impact-of-continuous-chromatography-mode-on-protein-a-lifetime/