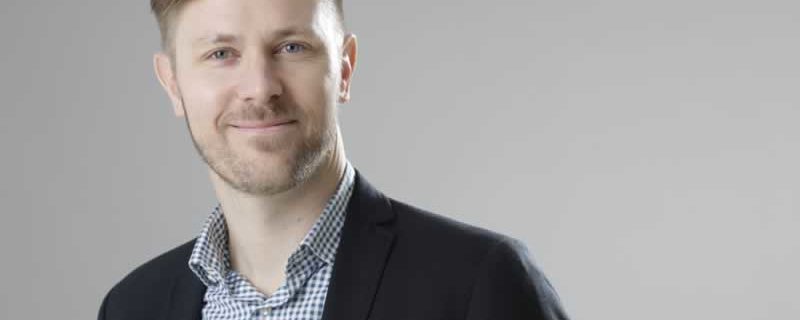
Resolving Large Scale Buffer Management Challenges
Podcast: Download (Duration: 11:59 — 16.5MB)
Subscribe: Apple Podcasts | TuneIn | Deezer | RSS | More
Show Notes:
We began the interview by discussing what inline conditioning is and how it can improve buffer management. Joakim explained that with inline conditioning, instead of making your buffer in the traditional way, by making it in the volume needed, you separate the individual components of the buffer, for example Acetic acid, NaAc, NaCl and water into separate stock solutions. The system then mixes these components in the required amounts, just in time, when buffer is needed. One of the benefits of the technology is that you can use the same stock solutions to make many different buffers of for example different buffer strength or pH depending on the relative portions of each component.
I then asked how inline conditioning differs from the concept of inline dilution. Joakim described how inline conditioning really takes the technology one step further. Inline dilution is a technology that works with a concentrated buffer of approximately the same composition as the final buffer, which is diluted with WFI to yield the final buffer. The concentrated solution needs to contain all the components of the final buffer and the pH has to be adjusted. Therefore, you need to prepare as many concentrates as you have unique buffers. You do save floor space as the concentrates are smaller in volume, but there is not the benefit of using the same concentrate for several buffers as with inline conditioning. Another thing to remember is that, when you dilute a buffer the pKa value typically shifts, meaning your concentrate needs to be adjusted for this shift. This will not be the case when you handle single component concentrates which are the input for inline conditioning. Inline dilution still has its place and is a good solution when you have a limited number of buffers or many different buffer components. And also typically when volumes are small to moderate. It is also important to note that inline conditioning can be used as an inline dilution system if there is a need.
We then discussed the main drivers for implementing this technology. One of the main drivers that Joakim shared is the ability to make fewer stock solutions than the buffers needed and in significantly smaller volumes. This enables the use of single-use bags. You also don’t have to adjust pH of the stock solution, as we mentioned earlier. All this combined means that you can save on facility space and remove all big tanks for buffer prep and storage. This provides a significant CapEx savings. It also takes considerably less time to make the stock solutions compared to buffers, which reduces the need for operators and also simplifies the logistics and handling of buffers.
I followed up with a question about limitations of the technology. Joakim stated that there are not really any limitations and it is possible to use the technology in most situations. The inline conditioning system is very flexible, so you can use a combination of techniques, including using final 1x buffers, inline dilution or breaking up the components into single component concentrates, all at the same time. Gradients are also straight forward with inline conditioning.
We then touched on flexibility and the different ways to implement inline conditioning. Joakim explained how it can be integrated in the unit operation or used as a standalone central buffer preparation station, a buffer kitchen, to provide the entire facility with buffers.
Next I asked about how you can be sure that the machine is preparing the buffers correctly, especially since having the right buffers are so important to successful purification. Joakim described how each customer buffer is made using control modes, which ensure that the mixing of components is controlled through advanced algorithms that regulate the flow of each component. The output is monitored through an independent set of monitors that essentially do an online release of the buffer. If the buffer is outside specifications the buffer is diverted to drain. With this you get all your buffer data as part of your result file and your process records, making it very simple to review. One other detail is that this system always aim to the specification, while traditional buffers typically are made to be inside specifications. There are also tests to do to verify that the correct stock solution is connected and connected to the correct inlet.
Last, I asked Joakim to summarize what he saw as the 3 key take aways from our discussion.
Joakim stated that first you can potentially reduce the buffer volumes to prepare, store and handle quite significantly. This leads to smaller footprints, smaller tanks and less labor. Many users can transition completely to single-use bags. It saves companies money, both on the CapEx and Opex sides.
Second, that the technology is flexible and can allow a wide range of buffers to be made using the same limited number of stock concentrates.
Third, that you can improve the control of you process due to the constant feedback inside the system, maintaining and checking that all parameters are inside specifications.
And if someone is interested, please contact your local sales representative and they will guide you through the process of finding out if inline conditioning is a good fit for your process.
For additional reading, please see:
Large Scale Buffer Management Solutions Page
Automated in-line buffer preparation from ready-made stock solutions in a mAb process step