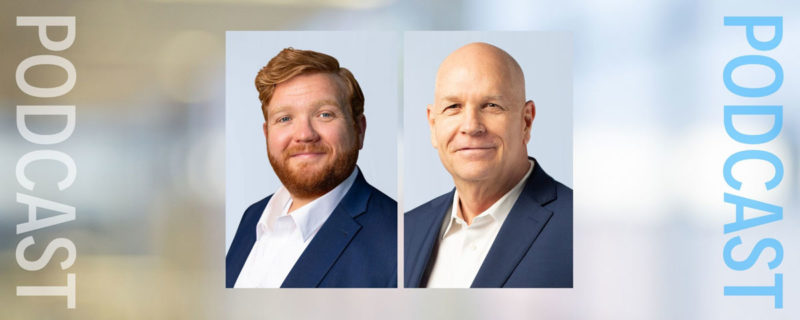
Single-use Mixers – Ensuring the Customization, Scalability and Supply Required for Success
In this podcast, we talked with Dennis Hodgson and Phil Sanders from Agilitech about the benefits of single-use mixers, dealing with supply chain concerns, ensuring scalability, and tailoring a mixer to meet specific process needs.
Benefits of Single-use Mixers
We began the podcast by talking about the overall benefits of single-use technologies for mixing. Dennis explained that single-use mixers are very versatile and can be used to replace stainless steel vessels within the manufacturing area. Single-use mixers all have the same advantages of other single use components, such as coming fully sterile and eliminating the need to steam and clean in place.
Dennis went on to say that another big advantage that single-use mixers have over stainless steel is the ability to customize. For example, a 500 L single-use mixer can be used with a virtually unlimited array of customized vessel configurations, which would include the inlet outlet, port configurations, sampling ports, vent filters, and various process analytics that can be added.
Next, we talked about adoption of single-use technology for mixing and possible concerns that customers might have. Dennis shared that a big concern recently has been supply chain shortages that have created limited availability and long lead times for single-use consumables. He said that he has heard from some clients that they have had to skip planned production batches because the single use bags that they needed to process the batch were not available. Phil added that supply chain concerns have caused some of their clients to think about moving to stainless steel systems to avoid any production delays.
Single-use Technologies Supply Chain Challenges
I followed up by asking what could be done to address single use supply chain issues moving forward. Dennis explained that Agilitech has the luxury of not being tied to any one supplier, so they can source from multiple vendors. This allows them the flexibility to move between vendors and load projects based on their capacity and lead times. This also allows them to make sure that they are offering competitive pricing because vendors know that they’re not the sole source of a component.
Ensuring Flexibility in Single-use Mixing
We then talked about mixers presenting unique challenges in that they are used for a variety of applications with many different demands. I asked how Agilitech can ensure that their single-use mixer has the flexibility needed for multiple applications. Dennis explained that because Agilitech isn’t tied to a single design, they are able to have conversations with the client to customize a solution for their needs. Their main goal is to make a product that meets the needs of the individual companies and their process. Additionally, they design their systems purposefully to handle many different capabilities such as sampling, analytical measurements, weight measurements, temperature control, etc. Because they use standard control hardware, their mixing vessels can easily be integrated into existing control systems such as Delta V or Wonderware through the available Ethernet IP connection. This allows users to read and write to certain control parameters.
I then asked about which options are available for customization on the single-use mixers. Dennis said that they can customize all the inlet and outlet ports with regards to port size, tubing length, connector type, etc. As far as the mixing units themselves go, they can be jacketed or not, have load cells or not, have probe analytics such as pH, conductivity, temperature, DOE, and optical density, so all those different analytical devices can be incorporated as well.
Phil added that if there are specific standards within an organization, for what control systems need to be installed on these systems Agilitech is flexible with Rockwell, Delta V, Siemens, all the major platforms that customers might need.
I followed up by asking about how these customization options affect the cost of these mixer systems. Phil said that frequently when customers hear the word customization or even tailored, they think that is going to drive the price up or maybe even drive the delivery time out. When Agilitech tailors a solution, it speeds up the delivery time and reduces the cost because everyone is on the same page and has alignment on what will be delivered. Agilitech works through all the issues up front with clients, so customers get exactly what they’ve asked for.
Single-use Mixer Scalability
We then discussed scalability and about how low volume mixers are difficult to find. I asked how Agilitech has been able to build scalability in their product line. Dennis described that their current sizes that range from 10 L to 650 L. He shared that their 10 L size has a minimum working volume of 1.25 L, which permits a process application such as a highly concentrated TF step to be able to be used with that mixing vessel. Additionally, because Agilitech has a total of seven different sizes, it allows customers to scale up their process for additional capacity using identically designed equipment. Levitronix is working on motors and impeller sizes that would permit Agilitech to offer up to a 3,000 L size in the future.
Easy Process Implementation
Next, I asked Dennis if he could talk about process implementation. He explained that each vessel comes with its own easy to use touchscreen interface that allows users to locally control the start and stop of the motor, change the setpoint of the speed on the agitator, and read local measurements for the weight, temperature, and other process analytics that are connected. Also, by using standard industrial hardware and standardizing on up-to-date future proof communication protocols such as Ethernet IP these systems can very easily be integrated into existing control systems.
Lastly, I closed the interview by asking Dennis and Phil if they had anything else that they wanted to share with listeners. Dennis said that the industry has gotten too used to there being too few options in the market and perhaps have started to shape their processes to align with what is currently available. At Agilitech, the aim is to shift that perception and put the power back with the end user to define their equipment requirements that meet their process instead of vice versa.
For example, changing the inlet and outlet size of your single-use mixing bag to better fit your process shouldn’t increase the costs and time to receive that bag significantly. End users should remain rigid in their requirements and process. Vendors should be the ones that remain flexible to meet the needs of the user.
Phil added that the solution should be plug and play to some extent. It shouldn’t be a monumental effort to implement a new solution in an existing process. A plug and play approach allows companies to get to market faster and to source components quicker.
To learn more, please visit Agilitech Single-Use Mixers.