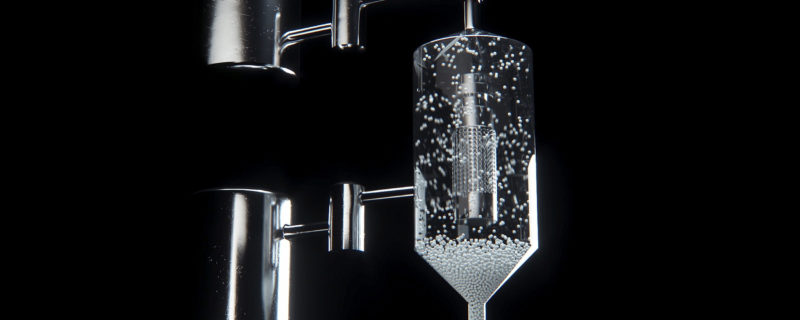
Strategies for Increasing Productivity and Reducing Cost of Chromatography in mAb Biomanufacturing
Increasing upstream titers, the need to increase throughput of existing facilities and the desire to reduce costs are just a few of the drivers forcing paradigm shifts in monoclonal antibody (mAb) downstream processes. These drivers are acutely felt in the selection of chromatography resins, as the purification step is often the source of bottlenecks and is costly.
Protein A has been the favorite choice for purification of mAbs for decades and there have been significant improvements since its first use. The selection of Protein A resins involve several factors relating to purification performance, these include productivity, buffer consumption, scalability, and process economy. In addition, new manufacturing strategies including continuous processing and hybrid options add additional criteria to selection.
Every product and facility presents its own unique process challenges and constraints. One issue is the increasing use of high titer cell lines. While producing large amounts of product in upstream, these processes are challenging existing facilities designed for lower titer processes. Facilities must adapt to handling a significant increase in product and buffer volumes. Thus, the industry needs new chromatography strategies and technologies to provide flexible purification solutions that can address increasing titers and do so cost-effectively.
Employing Uniform Particle Size
One technology designed to increase productivity at lower cost is the use of uniform particle size chromatography resins. These resins have demonstrated higher dynamic binding capacities and reduced buffer consumption. Thereby, lowering the impact on existing facilities.
Praesto® Jetted A50 is a next generation agarose resin manufactured using a proprietary jetting technology, developed by Purolite® Life Sciences, which produces resin beads with a very narrow particle size distribution. The combination of uniform agarose particles with a novel Protein A ligand (NGL-Impact™ A from Repligen Corporation) results in a resin with very high capacity at a wide range of flow velocities.
The Purolite jetting process entails using a membrane with very small, discrete orifices, through which the polymer is passed. This device is capable of producing uniform particle size chromatographic resins from ~15 to 250 micron. Cooled, and then hardened, the beads are then collected in a vessel. The process can run continuously and has been scaled up in Purolite’s plant for the past decade.
Subsequent process steps in jetting (cross-linking, derivatization) are similar to those for emulisified beads. The process is diagrammed below along with images showing the differences in the beads generated (Figure 1). The jetting technology results in beads that have a more uniform size when compared with the standard technology that instead generates a wide variety of bead sizes (Figure 2).
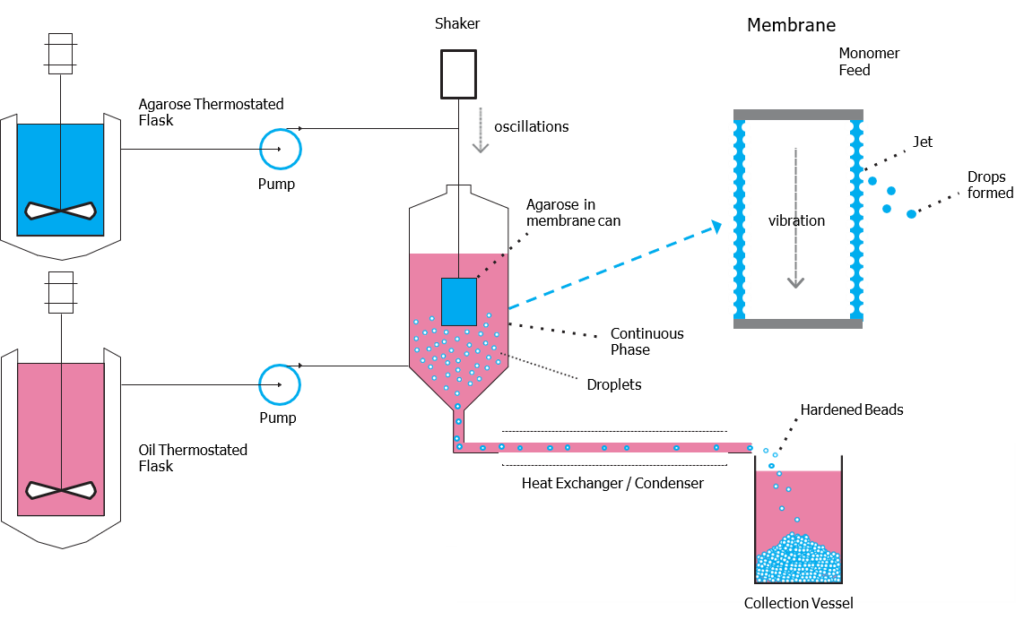
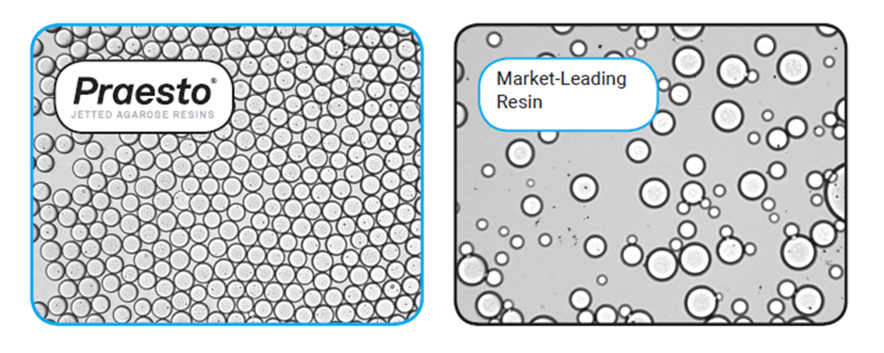
Additional advantages of Praesto® Jetted A50 columns include:
- More consistent packing characteristics
- Better kinetics
- Improved resolution
- Longer resin lifetime
To learn more about jetting technology and the benefits of uniform particle size resins, please see “Advances in Bioprocessing: The importance of uniform particle sizes in protein A chromatography”.
Process Intensification – SMART Cycling Strategies
Another approach to improving purification is to employ new strategies for increasing productivity; these are often part of a larger plan for overall process intensification. To demonstrate how the Praesto® Jetted A50 can be used as part of a process intensification strategy, Purolite conducted studies to look at four SMART cycling strategies and how each strategy impacts productivity and process economy. The study results were presented in a webinar, “SMART Cycling: Strategies for Improved Productivity, Buffer Consumption, Scalability and Process Economy in Downstream mAb Purification”.
SMART Cycling Strategies
To illustrate the impact of different strategies, Purolite conducted process economy calculations based on a standard purification from a 2000 L cell culture reactor expressing 5 g/l with resin loading to 80% capacity, using MabSelect™ SuRe LX as the benchmark resin. A diagram of the variables tested can be seen in Figure 2.
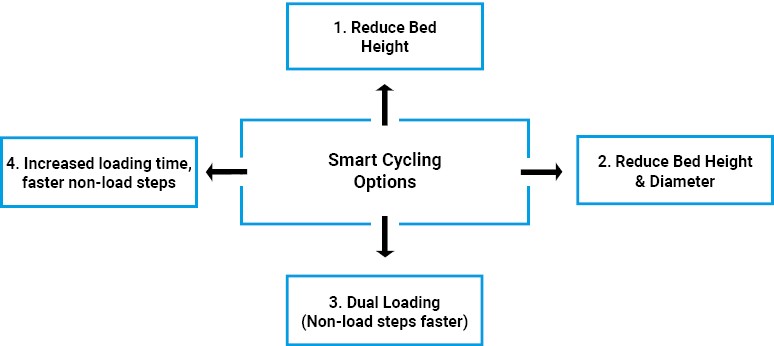
SMART Cycling for Productivity
Reduced Bed Height
One advantage of this scenario is that it can fit into an existing batch process protocol with only the bed height changed. By using the Praesto® Jetted A50 and reducing the column size by half, Purolite was able to double productivity and achieve a 65% reduction in resin costs when compared to the benchmark resin. All other process conditions, volumetric flow rate and facility time remained the same.
SMART Cycling for Cost Efficiency
Reduced Bed Height and Column Diameter
In this scenario, the bed height and column diameter were reduced for a significant reduction in column volume. They used similar levels of buffer consumption and a slight increase in processing time (~3 hours). The result was an 80% reduction in resin costs and a doubling of productivity.
SMART Cycling vs. Conventional
Reduced Buffer Consumption
In this approach, buffer consumption is reduced by 40%. Praesto® Jetted A50’s small uniform beads permit rapid diffusion and less dispersion for an overall reduced buffer requirement. This approach was achieved in a similar processing time, but with ~3x gain in productivity and 80% reduction in resin costs.
SMART Cycling – Buffer Consumption and Productivity
Dual Loading Model
Lastly, the dual loading model illustrates the impact of combining a “dual flow” rate strategy to maximize sample loading with an optimized wash protocol. Dual flow means that the feed material is loaded at two different residence times to fully utilize the high dynamic binding capacity of resin while maintaining a high productivity. The smaller and more uniform particles developed using the jetting technology results in improved mass transfer allowing less buffer to be used for the different wash steps. Using this strategy, maximum capacity utilization and greater than 20 % reduction in buffer volume were achieved.
For full data sets, please see SMART Cycling: Strategies for Improved Productivity, Buffer Consumption, Scalability and Process Economy in Downstream mAb Purification
Summary
Technologies like the Praesto® Jetted A50 resin and novel approaches for the chromatography step provide the flexibility needed to meet the increasing demands placed on downstream processing. These novel approaches have been shown to provide increased productivity, decreased buffer consumption and lower cost for consumables. These strategies and others will be needed to meet the evolving demands for mAb manufacturing and enable more efficient use of both existing and future downstream facilities.
For more webinars on chromatography resins and purification strategies, please see the Purolite Digital Learning Series