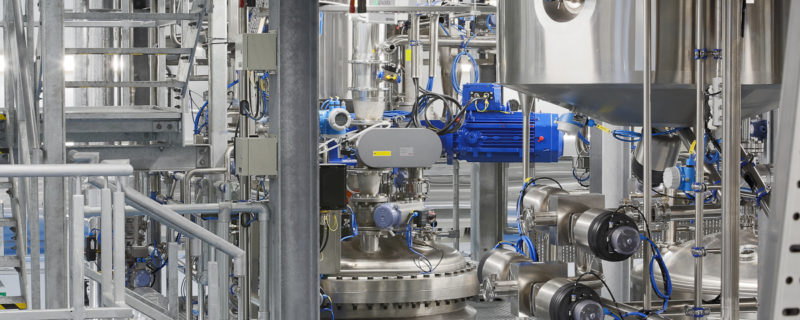
Supplier Qualification and Material Selection – A Case Study of Biopharmaceutical Resin Manufacture
To ensure a safe and continuous supply of life-saving biopharmaceuticals, raw materials for biomanufacturing must be selected carefully and suppliers evaluated with much scrutiny. Several instances of drug shortages as the result of either a raw material shortage or contamination reinforce the need for thorough evaluation. Ensuring a reliable supply and the quality of the materials selected is of paramount importance.
To help manufacturers make decisions related to material selection and supplier qualification, they must rely on a careful evaluation of a suppliers’ financial stability, capacity, quality history, material performance and contingency plans. However, a one time evaluation is not sufficient in that any changes that a supplier might make in their source, their production process, or a myriad of other items could impact the raw material quality and thus would impact drug manufacturing and ultimately could impact drug availability to patients. Thus, raw materials require continuous monitoring using a drug life cycle approach.
Supplier Qualification – A Case Study of Biomanufacturing Resin
Since material selection and supplier qualification is such a complex topic, I enjoyed a recent webinar, “Material Selection and Supplier Qualification for Biopharmaceutical Manufacture: Resins,” which provided key considerations for supplier qualification and also presented a case study of biomanufacturing resin qualification. I thought this was very useful information for both biomanufacturing companies who are routinely engaged in supplier qualification and suppliers who are regularly audited.
https://youtu.be/8iZ5Robc-c4
The presentation began with Duncan Low, M.A., PhD, Independent Consultant, Claymore Biopharm LLC, who provided excellent experience, as he had been involved with supplier qualification from both the end user and supplier perspective. He began by explaining what he thought was important in supplier qualifications. He said that supplier partnership is a key success factor; manufacturers should have sufficient oversight of suppliers and a structured approach should be used that considers both application and risk.
He shared a diagram that explains the holistic approach he recommends (Figure 1).
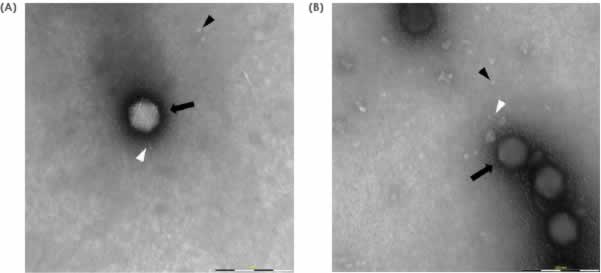
Dr. Low explained that the audit process requires significant resources to qualify candidate material. In light of this, it is important to take a life cycle approach, as material and supplier qualification require continuous monitoring. Formal audits, which are one part of the approach, are intensive. Another approach is to conduct a shared audit, which is a single very detailed audit that can be shared by the supplier with multiple companies. This provides benefits to both the manufacturer and supplier in terms of time and resources. In figure 2 below, he presented key elements to consider for supplier selection, material qualification and suggestions for both monitoring and continuous improvement.
Dr. Low also stressed the importance of pre-work prior to any qualification or audit in order to maximize efficiency. Critical pre-work tasks included:
- Get the legal stuff done (confidentiality)
- Require information about special procedures (e.g. safety, clothing, etc.)
- Provide a detailed agenda on topics to be covered and why
- Request as much general and specific information as possible prior to the visit, in order to focus on visit specific topics on-site
- Company presentation
- Technology presentation
- Regulatory information
- Risk management
- Supply chain management
- Use standardized Requests for Information (RFI)
Case Study of a Supplier Qualification – Purolite’s Biomanufacturing Resin
At this point, the presentation moved into the case study where Dr. Low conducted a supplier qualification of Purolite Life Sciences’ agarose-based Protein A and Ion Exchange resins. To begin the discussion, Duncan Sinclair, Agarose Plant Manager forPurolite Life Sciences presented background information on their resin manufacturing technologies.
Purolite has two types of agarose manufacturing technologies; batch wise emulsification and jetting technology. Duncan stated that batch wise emulsification is considered the “industry standard” and has been used by Purolite since 1984. They are able to produce styrenic and methacrylate resins in up to 10,000 liter batch sizes in 20,000 liter process vessels using this method.
Their jetting technology is a novel proprietary technology for improving particle size control and distribution. The Purolite jetting process – membrane or ‘can’ jetting – entails using a membrane with very small, discrete orifices, through which the polymer is passed. This device is capable of producing uniform particle size chromatographic resins from ~15 to 250 micron. Cooled, and then hardened, the beads are then collected in a vessel. The process can run continuously and has been scaled up in Purolite’s Romanian plan for the past decade. To date their largest continuous jetting run has been 9 days of production with 45 tons of resin produced.
Subsequent process steps in jetting (cross-linking, derivatization) are similar to those for emulisified beads. The process is diagramed below along with images showing the differences in the beads generated (Figure 3). The jetting technology results in beads that have a more uniform size when compared with the standard technology that generates a wide variety of bead sizes.
Duncan goes on to describe Purolite’s method for maintaining control over each process step at various scales. The level of automation increases as scale goes up and technology transfer has been key to ensuring consistent performance from R&D through full-scale production.
Next Duncan described how Dynamic Binding Capacity (DBC) is a key parameter for customers and that Purolite has a deep understanding of all of the parameters affecting DBC. They use this understanding to generate alkaline stable high capacity Protein A resin that has been benchmarked against market leading resins (Figure 4).
In addition, they have demonstrated acceptable batch-to-batch variation in DBC across multiple production scales (Figure 5).
At this point in the webinar, Dr. Low resumes speaking and adds his thoughts on the benefits of jetting technology. The benefits are largely based on the uniform particle size.
Key benefits include:
- Better chromatographic performance (efficiency/resolution, DBC)
- Lower back pressure
- Better packing reproducibility
- Tunable particle size, continuous manufacture
- Multicolumn chromatography
With respect to the audit process, Dr. Low shared that the Purolite staff was impressively open in discussing manufacturing technology and that they had a good understanding of the critical parameters. In addition, they were able to explain manufacturing deviations and had a commitment to further refinements with increased experience. He found the jetting technology to be scalable and transferrable.
Dr. Low then discussed the detailed steps he took in evaluating them as a supplier. He made it clear that he believes the audit begins with first impressions and those usually start in the parking lot. He stated that the facility should have good general maintenance, be free of obvious location risks, good access for both incoming and outgoing of shipments and emergency services, and segregation of flammable solvents.
Next, he detailed his steps for auditing the warehouse and stated that in an audit you should be able to follow the trail of incoming materials from start to finish.
Next, the manufacturing plant layout was evaluated and he stressed key areas that should be included:
- General layout, size
- Expansion capabilities
- Segregation of areas
- Grey zones – services, maintenance
- Materials flow
- Quarantine areas
- Air quality
- Pest control
From there he moved on to assessing the manufacturing process and plant controls for their effectiveness. This included evaluating capacity, cycle time, equipment maintenance redundancies, environmental controls and documentation. For plant controls, he recommends reviewing operating hours and parameters, staffing, alarms and in-process controls.
For the development labs he says the primary thing to evaluate is equipment capability and fit for purpose and for the QC labs it is sizing and fit for purpose plus management of samples. Lastly, the finished goods area needs to be looked at for packaging and characterization testing, shipping methods, temperature requirements, etc.
Conclusion
In conclusion, Dr. Low emphasized that Purolite had an impressive audit. Highlights included that they had made significant investment and a tangible commitment to resin manufacture and possessed innovative manufacturing technology. They demonstrated solid technical capabilities in the design, development, manufacture and characterization of their resins and good technical skills in support of the product. Another key feature was that they have strong relationships with sub-suppliers who provide critical materials. Lastly, their pricing strategy is very attractive.
For more information, please see Jetting Technology