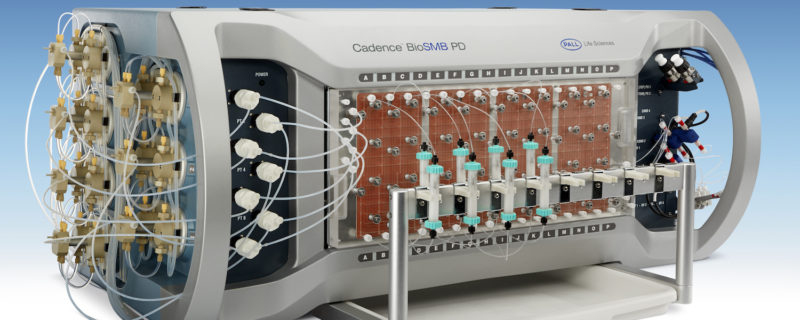
Achieve Integrated and Scalable Continuous Chromatography
Over the last decade, advances in the upstream processing of monoclonal antibodies (mAbs) has resulted in higher bioreactor titers. With increasing titers, the production bottleneck has shifted to downstream processing. Hence, the biopharmaceutical industry has reached a milestone where the need for higher throughput in downstream processing is leading to the adoption of more efficient multi-column continuous (MCC) counter-current chromatography systems which increase overall productivity while significantly reducing consumables costs.
Advantages of multi-column chromatography
A major distinction between batch (single column) chromatography and MCC is in the load step. In batch chromatography, the capacity is highly dependent on residence time during loading. To achieve high capacities, long residence times are required. In MCC, two or more columns are connected in series during the load step. The primary function of the additional load column(s) is to enable the overloading of the first column that receives feed, while ensuring all product is captured. This allows loading of the first column in the series beyond product breakthrough and provides an improvement in capacity utilization. Thus, the multi-column strategy allows for high capacities at very short residence times during loading.
Continuous Chromatography is now possible for clinical manufacturing
To provide continuous multi-column chromatography, Pall launched the Cadence™ BioSMB platform. This platform provides a complete solution to enable continuous MCC processes from process development (PD) through to commercial manufacturing processes.
Pall identifies two key benefits in adopting the BioSMB technology.
Easy scale-up between PD and manufacturing
- Transferable recipes
- Identical flow path architecture
All benefits realized at PD transferred to manufacturing:
- High productivity
- Lower buffer consumption
- Shorter process times
- Reduced volumes of chromatography sorbent required
Direct scale-up from PD to Process
The Cadence BioSMB technology incorporates an entirely singe use flow path for MCC, utilizing a unique integrated single use valve cassette. The technology enables a significant increase in specific productivity of a process resulting typically in a 3-5x reduction in volume of chromatographic sorbents and lower buffer consumption. This makes single-use Cadence BioSMB systems the first choice for flexible manufacturing sites, with the Cadence BioSMB PD system serving as a development platform which is directly and easily scalable to the Cadence BioSMB Process 80 and Cadence BioSMB Process 350 systems for cGMP manufacturing.
For more Downstream Column Articles on this Topic, please see:
https://downstreamcolumn.com/look-current-state-continuous-bioprocessing/