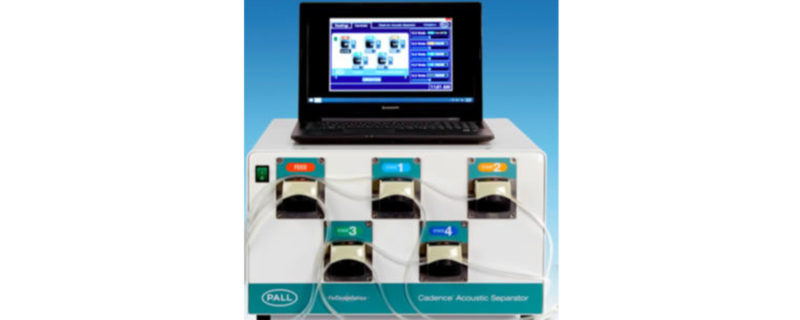
Clarification Using Acoustic Wave Separation Offers Advantages including -Continuous Process Solution
Background
The harvest and clarification of cell culture bioprocess fluids removes cells and cell debris and provides clarified cell culture harvest fluid for downstream purification. The success of the clarification step can greatly impact efficiency and ease of downstream purification. Improvements in cell culture techniques have resulted in both higher cell densities and higher product titers, and so the clarification step has become more challenging. As a result, there has been a need to develop technologies to improve the efficiency of harvest and clarification. In addition, the interest in moving toward a continuous process has also spurred advances in clarification because traditional clarification steps like centrifugation and depth filtration are typically done in batch mode.
Acoustic Wave Separation
In response to the evolving needs in clarification, Pall recently launched the Cadence Acoustic Separator as an alternative clarification method. The Cadence Acoustic Separator (CAS) is based on acoustic wave separation (AWS) technology that was originally developed by FloDesign Sonics.
How Acoustic Wave Separation Works
In short, AWS technology applies acoustic forces across a countercurrent flow of bioprocess fluid to generate 3D standing waves that trap cells at their nodes leading them to agglomerate and eventually sediment as they lose buoyancy. In my opinion the best way to truly understand the acoustic wave technology is to view it in action. This video provides an animation of the process:
https://www.youtube.com/watch?v=YOr7AGGx3MI
Key Advantages of the Cadence Acoustic Separator (CAS)
Pall has identified several key areas where the CAS system can provide benefits. I have highlighted some of these below, but for more information and data, please see – Cadence Acoustic Separator
Efficiency
The CAS system is optimized for CHO cells at cell densities of 20-50 x 106. However, it can be applied to a range of biologic products regardless of variability in particulate concentrate or cell culture density. In the area of CHO cell culture, the system has demonstrated efficient performance with high yields, reproducible results and consistent purity profiles. Clarification efficiency is provided by Pall in Figure 1.
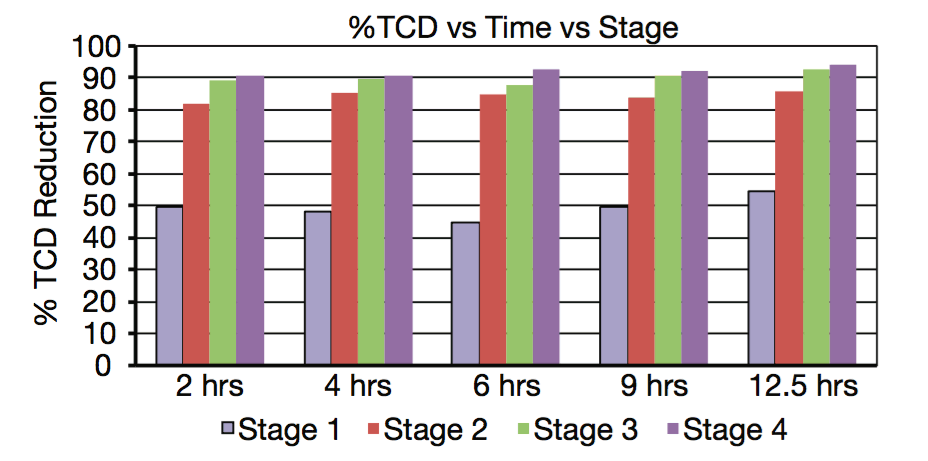
A nice feature of the CAS system is the smoothness with which it moves from process development scale to full-scale production. Once optimized, the process can scale directly based on optimal flow rates identified for the primary separation using the CAS system and throughput for the secondary polishing depth filter selection.
Improved Economics
Pall has presented data that shows when compared to large scale depth filtration the CAS system allows for a 75% reduction of both the filtration area and buffer volume requirements. This results in reduced tank sizes and a lower operational footprint. Also, due to lower turbidity when using CAS, there is a reduction in the secondary depth filter area requirements and associated conditioning and flush buffers. Pall has provided an example of anticipated process requirements for a 1,000 liter CHO run in Table 1.
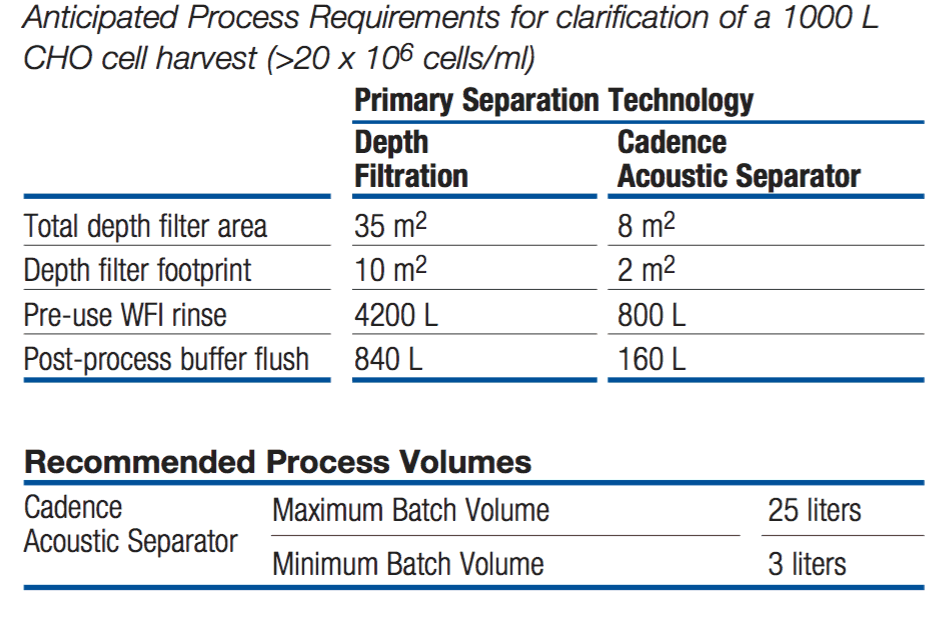
Enables Continuous Process
The CAS system can be set up to provide continuous removal of CHO cells and cell debris and is single-use. This is important because centrifugation and depth filtration are typically operated in batch mode, which requires product hold steps during the process. The continuous feed of harvested cell culture fluid provided by the CAS system can be directly loaded onto a continuous chromatography platform, thereby providing a continuous operation from bioreactor through chromatography.
For more information, please see – Cadence Acoustic Separator