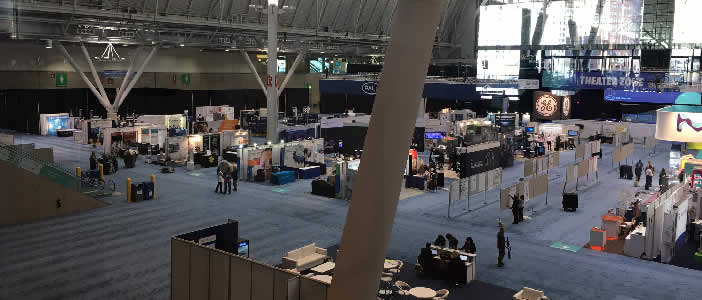
2017 Biotech Week Boston – Downstream Coverage Highlights
Last month, Boston Biotech Week featured interesting content with a wide range of issues, from cell culture techniques to commercialization and everything in between covered. Talks focused on improving the manufacturing process for biopharmaceuticals and cell therapies, enabled industry networking opportunities, and provided the chance to see the latest products and technologies.
One area that I focused on was downstream manufacturing including recovery and purification, viral safety, and drug product manufacturing including fill/finish.
Recovery and Purification
One of the most discussed topics for this year was overcoming bottlenecks, particularly with intensification processes. Other hot topics included: innovative chromatography resins, product specific resins and purification of next generation therapeutics.
Other topics included:
- Removal of host cell proteins
- Novel harvest methods and clarification techniques
- Employing process modeling in downstream
- Continuous downstream purification
Selection of talks and announcements:
Flow through versus bind and elute: An alternative strategy for improved robustness and manufacturability for a challenging cation exchange chromatography
Jessica Prentice, Scientist I, MedImmune, gave and interesting talk titled “Flow through versus bind and elute: An alternative strategy for improved robustness and manufacturability for a challenging cation exchange chromatography.” The presentation described a case study where cation exchange chromatography (CEX) was used in flow through mode for a challenging monoclonal antibody bind and elute CEX case. What Jessica and her team found was that operating CEX using flow through mode offered a more robust alternative and wider operation space compared with bind and elute. Flow through mode also improved manufacturability including savings on resin volume, buffer volume, and number of buffers used. They found also that they were able to achieve increased throughput and overall simpler operation. Plus, flow through CEX can be easily incorporated into continuous manufacturing processes.
Addressing the risk of bioburden and the need for increased productivity in protein A chromatography
Jonathan Rocye, Business Leader – Chromatography Resins, GE Healthcare Life Sciences, presented a talk titled “Addressing the risk of bioburden and the need for increased productivity in protein A chromatography.” Jonathan began the presentation by discussing challenges and opportunities for protein A step improvements. These included:
- Increasing upstream titers may make Protein A step a bottleneck
- Protein A chromatography columns are too large, limiting the use of prepacked devices and creating a mismatch to subsequent downstream operations.
- Protein A chromatography columns are more prone to bioburden contamination due to heavy impurity load and weak tolerance towards the most efficient cleaning-in-place solutions.
- Regulatory agencies are increasingly asking if manufacturers understand the sources of bioburden and have them under control.
To address these challenges, GE has developed a next generation protein A chromatography resin, the MabSelect™ PrismA. The MabSelect PrismA was designed for improved alkaline stability, which permits the use of new tools for cleaning and sanitizaiton. These tools include up to 1.0 M NaOH and the oxidizing agent Peracetic acid (PAA) that has been shown to effectively address spore forming bacteria. MabSelect PrismA was also designed for increased binding capacity, which provides both higher productivity and increased mass throughput.
Cost modeling of the downstream bioprocessing design space
Another interesting talk titled, “Cost modeling of the downstream bioprocessing design space,” was given by Mark Schofield, Ph.D., Senior R&D Manager, Pall Life Sciences. In the talk, Dr. Schofield describes some of the challenges facing biomanufacturing including cost pressure, competition, and the rise of biosimilars. One way to address these challenges is to employ continuous bioprocessing.
To identify the most cost effective downstream monoclonal antibody purification strategy, Mark and his team modeled different unit operation sequences using BioSolve. The process types modeled were stainless steel, single-use, and integrated continuous bioprocessing. They also included in the model whether the operation was clinical or commercial manufacturing. BioSolve is a modeling platform, which includes customizable process sequences, detailed manufacturing cost calculations, and allows new technologies to be analyzed relatively easily.
Mark described in detail the various modeling scenarios, but in this high-level overview, I will just provide a summary of the findings. Based on the set of assumptions that were used with the modeling, the integrated continuous bioprocessing platform had the lowest cost of goods across 78% of the entire space explored. Major sources of savings in the process were the Cadence BioSMB system, which offered reduced chromatography sorbent volume and buffer reduction. It also offered flexibility of column configuration that provided the potential for even further savings. Another key part of the savings was the Cadence Acoustic Separator that reduced capital and the cost of consumables.
Purolite Life Sciences’ features proprietary ‘jetting’ technology for manufacturing agarose beads
Recently Purolite has developed proprietary ‘jetting’ technology to produce uniform agarose beads with a very narrow particle size distribution. This innovative manufacturing process removes the need for extensive and costly screening and improves yields significantly. Resins manufactured using this technology demonstrate enhanced performance characteristics including: enhanced pressure/flow properties, improved resolution, and uniform particle sizes. The ‘jetting’ technology also dramatically reduces lead times when compared to conventional agarose manufactures which are often upwards of 9 months for large volume commercial batches. The use of ‘jetting’ technology has been so successful, that today Purolite produces 1,000 m3/year of synthetic resins using this technology.
Using ‘jetted’ agarose beads allows their customers to deliver more efficient processes and increase productivity thereby. ‘Jetting’ is also a continuous manufacturing process that significantly produces beads more efficiently with very high yields, and since the beads are uniform in size it removes the need for sieving which generates considerably less waste. Another key advantage with this new technology is that it is more environmentally friendly since it eliminates the need for organic solvents compared to batch processing. The environmental benefits of ‘jetted’ agarose enables their customers to achieve their corporate goals of sustainability, and allows Purolite to bring to market beads smaller than 45 µm that would otherwise be uneconomical to manufacture at the bioprocess scale. The Downstream Column, recently covered this technology in a Cool Tool feature – ‘Jetting’ technology for manufacturing agarose beads with enhanced performance characteristics
The company’s 35 years of resin knowledge, their customer-focused approach and global manufacturing capacity is featured in this video which highlights their proprietary ‘jetting’ technology and dedicated manufacturing facility.
https://youtu.be/x3OJrmVxJz8
Viral Safety
Two of the most discussed topics for this year were raw material qualification and scale up/scale down challenges.
Other topics discussed included:
- Taking a holistic approach to virus safety
- Upstream virus filtration step
- Virus filtration and continuous bioprocessing.
Drug Product Manufacturing and Fill-Finish Processing
This is by no means an exhaustive list, but some highlights of the talks I attended include:
- Closed systems
- Use of predictive modeling
- New fill/finish technologies
- Improvements in freeze, storage and thaw methods
- Endotoxin control
I will cover several of these areas in more detail in the coming weeks – stay tuned.