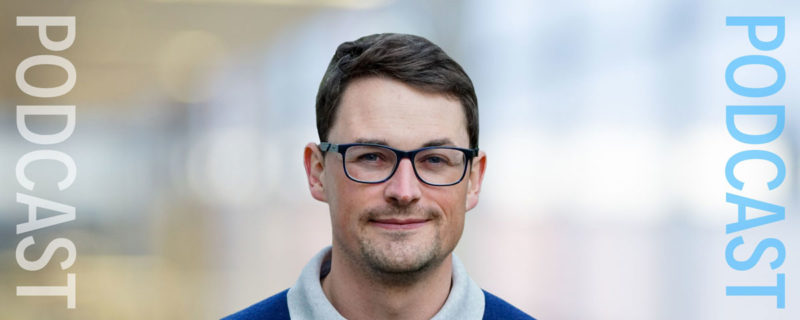
Flexible single-use mixers are key to achieving a next level mixing experience and reducing delivery lead times
Podcast: Download (Duration: 16:22 — 13.1MB)
Subscribe: Apple Podcasts | TuneIn | Deezer | RSS | More
In this podcast we spoke with Klaus Kienle, Global Product Manager for the Mixing portfolio at Pall Corporation about the latest mixing technologies including single-use solutions, the need for increased flexibility, and a more standard vendor agnostic approach.
The Role of Mixing in Biomanufacturing
I started the conversation by asking Klaus if he could talk about the role that mixing plays in biomanufacturing and current challenges in this area. Klaus explained that mixing is an omnipresent process. It starts with upstream buffer media and ends in fill and finish. It is an important part of manufacturing across several modalities, including monoclonal antibodies, mRNA based vaccines, gene therapies and various other processes. Across these various applications, flexibility is key, and it is also the primary challenge for the future. He continued by saying that Pall customers have expressed that they want increased flexibility, better lead times, and less supplier dependency in the future.
Advancements in Mixing
Next, I asked about the latest technological advancements in mixing. Klaus stated that the latest advancements are moving towards tackling the flexibility challenge, which means supplying solutions that are available with shorter lead times and are more vendor agnostic, so they fit with other vendors’ manifolds and full sets. This is consistent with the recent launch of the Allegro™ Ready Standard Solutions from Pall, which is not only limited to mixers, but also includes storage transfer sets and other segments. Pall has launched this new standard set ranging from a 30 liter mixer up to a 3000 liter mixer.
I continued the discussion by asking if he could talk a little bit more about some of the additional advantages of this set of new standards. He described how these standards are ready to go, so if a customer is asking for a manifold, there is no time required to generate a drawing or waiting for pricing back, resulting in a short lead time. Pall is working towards having these standards available off the shelf, reducing lead time further with availability in the range of single digit weeks, depending on manufacturing and where the customer is located. He shared that Pall has invested $1.5 billion to increase capacity and reduce lead times.
Single Use Mixing
I then asked him about some of the remaining challenges that exist with single use technologies. Klaus explained that one of the main challenges that the remains in single use is sustainability, especially since it consists predominantly of plastic components. However, there was a recent publication in New Biotechnology, authored by biopharmaceutical companies, “Streamlined life cycle assessment of single-use technologies in biopharmaceutical manufacture.” It makes the case that single use technology is providing better sustainability in the biopharmaceutical process because single use technology allows customers to use more intensified processes, thereby increasing the efficiency per consumable. Single use technologies also support a closed process and reduced clean room requirements resulting in lower energy requirements.
This is in line with the new standard designs from Pall, where the filtered product line is fully closed and processing ready. For instance, now the powder port on these designs ensures a closed and controlled environment. This then allows bioprocessing companies to lower the cleanroom environment requirements, which translates to significant energy savings.
Modular Mixing Approach
I continued our discussion by asking Klaus about a recent white paper published by Pall and Lonza, that highlighted a modular mixing approach. (need paper link) He described how a modular approach can give customers the flexibility that they are looking for to adapt to new requests, especially in the contract manufacturing organization (CMO) environment. Global CMOs are producing product for developers and as a result, they are frequently changing the product they are manufacturing. Their facility needs to be set up with the greatest degree of flexibility to adapt to changing needs as well as short notice production demands. For example, the need to be able to respond under short notice was clearly seen in the push to produce the COVID-19 vaccine. If a CMO gets this request and they’ve built their facility with a modular approach, systems could be interchanged easily. This would allow them to adapt quickly from a monoclonal antibody process to an mRNA process. A modular approach can also save companies on CAPEX as some consumables they will have in stock. The paper illustrates the ease of use of Pall mixer systems and their flexibility, which allowed a fast change over without buying new equipment.
What to Consider when Selecting a Mixing System
Next Klaus provided advice for listeners about what end users should be considering when selecting a mixing system. He replied that there is a message right now from some suppliers that one size fits all solutions are the best option, but the reality is simply that most processes are so unique and so variable that one size fits all doesn’t work. Pall takes a different approach by offering four different mixers providing a variety of solutions depending on the process. For example, if a customer needs a very powerful mixer, Pall offers the magnetic mixer, but if they need a shear sensitive one, they recommend the LevMixer® system. Because they utilize the same mixing tank, a simple change of the drive unit makes the equipment ready for either the high power demand of the magnetic mixer or the shear sensitive mixing of the LevMixer system. This flexibility allows customers to quickly adapt their entire facility towards a specific process without exchanging the big capital systems.
Before we wrapped up the interview, I asked Klaus if he had anything else that he’d like to add for listeners. He told me that the Danaher philosophy is listening to the voice of the customer. Pall embraces this and takes it very seriously. This means that Pall reaches out to customers to ask what their specific needs are and how they can improve. One key slogan within Danaher is continuous improvement and Pall has applied that to their product portfolio by continuing to work on providing flexibility and interchangeability, not just within Pall, but future interchangeability between several technologies in the market. He added that his personal goal is to deliver the next level mixing experience, which in some cases is not the next level technology. It might be the next level of flexibility instead of the technology, but in the end, the bottom line is that the customer is experiencing happy mixing.
For more information, please see the white paper Trends in Single-Use Mixing Technologies for Biomanufacturing