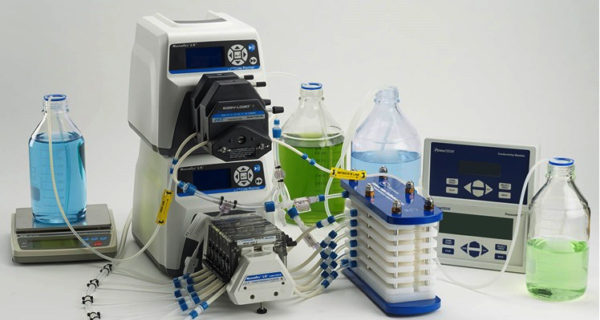
Inline Diafiltration Closes the Gap for End-to-End Continuous Bioprocessing
Diafiltration, while fulfilling several functions in protein purification, has also presented a major obstacle in achieving continuous biomanufacturing. Technologies launched over the last decade have moved the industry closer to completing an integrated end-to-end continuous bioprocessing platform; however adequately addressing continuous final ultrafiltration/diafiltration of drug substance has been challenging. Now, inline diafiltration offers a solution to both traditional bottleneck hurdles and continuous biomanufacturing platform gaps.
Inline Diafiltration Solution
The Cadence™ inline diafiltration (ILDF) device launched late last year, is specifically designed to meet the needs of continuous bioprocessing by supporting key diafiltration applications. These applications include: buffer exchange for final drug substance, desalting or buffer exchange before or after column chromatography, and small molecule contaminant removal.
Cadence Inline Diafiltration Workflow
The Cadence ILDF utilizes Pall T-series cassettes as the building blocks for the module. The modules are provided with either a Delta regenerated cellulose or Omega™ polyethersulfone membrane. This design ensures accurate scalability, proven selectivity, and low protein binding attributes commonly associated with these membranes. Additionally, flexibility has been addressed, as modules are available in a range of size formats to accommodate various processing volumes and process applications.
Key Benefits Include:
- Enable continuous processing – Continuous diafiltration is facilitated through the use of staging, providing repetitive dilution / concentration cycles without a re-circulation loop and with significantly smaller system hold-up volume.
- High removal factors – The Cadence ILDF technology allows for removal factors of ≥ 3-log. Dialing in the number of diavolumes is easily achieved by adjusting the flow rate on the buffer addition pump and performance is stable over extended operation times.
- Optimize processing of highly shear-sensitive products – Processing results in only one pass through the pump and module, therefore reducing shear exposure. Further benefits are achieved by eliminating any mixing or foaming issues associated with the feed tank.
- No holder required – Cadence ILDF modules come assembled, and the cassettes and manifolds are configured between two end plates with no extra holder needed. A pre-configured tubing manifold is also provided. Simply torque the device to the recommended setting and attach the tubing manifold to a feed pump and diafiltration buffer pump.
Performance Data
Cleanability and Re-Usability of Cadence Inline Diafiltration Modules
In a recent study, Pall found that the Cadence inline diafiltration modules could be re-used several times with minimal change in performance. See Cadence inline diafilatration study for more details.